Repairing Cast Aluminium: Techniques and Considerations
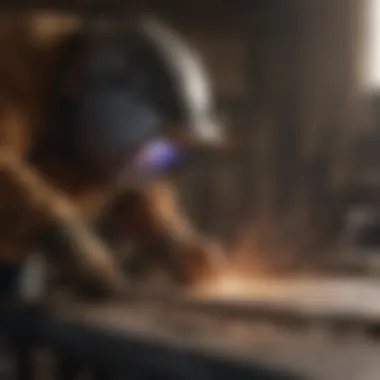
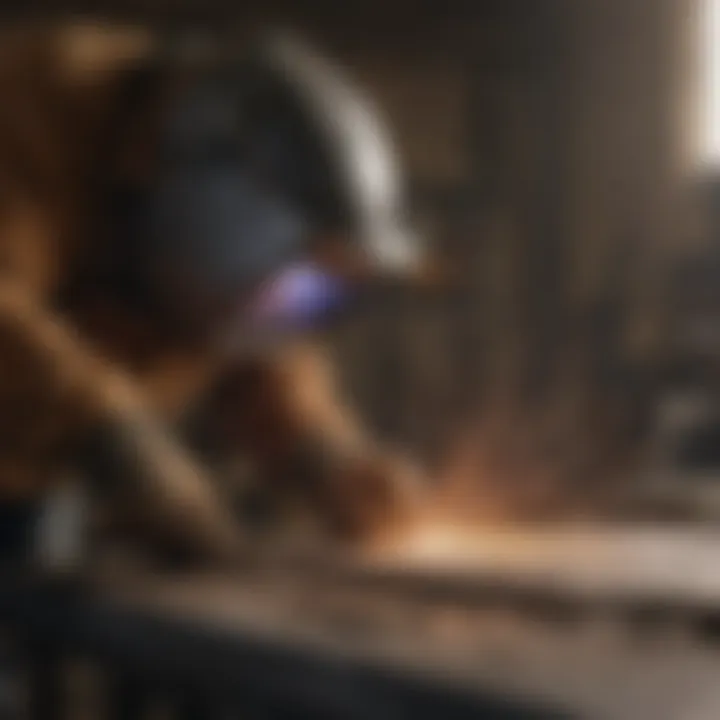
Intro
Repairing cast aluminum is a crucial area of focus for various industries, especially in agriculture and horticulture. Cast aluminum's unique properties, such as light weight and resistance to corrosion, make it a sought-after material. However, repairing it presents distinct challenges. Improper methods can lead to further damage or ineffective repairs, which can result in increased costs and safety risks. This article delves into the fundamental aspects of repairing cast aluminum, covering essential techniques and considerations that practitioners need to bear in mind.
Key Concepts and Terminology
Definition of Terms
Understanding the terminology surrounding cast aluminum repair is essential. Here are a few key terms:
- Welding: A process that joins materials by melting them together.
- Brazing: A method of joining metals using a filler material that has a lower melting point.
- Adhesive Bonding: A technique using adhesives to bond components without altering their structure.
- Metallurgy: The study of metals and their properties, crucial for understanding how aluminum behaves under heat and stress.
Importance in Agriculture
In agriculture, cast aluminum components are prevalent in machinery and structures. Equipment such as irrigation systems, machinery frames, and attachments often incorporate this material. Effective repair techniques can enhance the longevity of such machinery, reduce downtime, and minimize replacement costs. Thus, understanding how to repair cast aluminum effectively can provide significant advantages to farmers and agriculture enthusiasts.
Current Trends and Innovations
Technological Advancements
Recent advancements in welding and repair technologies have transformed the landscape of cast aluminum repair. Newer welding processes like TIG (Tungsten Inert Gas) welding offer precision and adaptability. Furthermore, advancements in filler materials have improved compatibility with various grades of aluminum, creating stronger bonds during repairs.
Sustainable Practices
The push for sustainability has prompted industries to rethink their repair strategies. Instead of replacing damaged components, which often involves significant waste, repairing cast aluminum items offers a more environmentally friendly alternative. Practices like using recycled aluminum for repairs or selecting eco-friendly adhesives are becoming commonplace, reflecting a broader commitment to sustainable agriculture.
Best Practices and Techniques
Step-by-Step Guides
Repairing cast aluminum can be accomplished using several methods, depending on the damage's nature:
- Assessment: Carefully inspect the damaged area to determine the best repair method.
- Preparation: Clean the surfaces thoroughly to remove dirt, grease, or oxidation.
- Welding/Brazing: If welding, select the appropriate welder and filler material. Ensure to follow safety measures during the process.
- Adhesive Bonding: For minor cracks, prepare the adhesive according to manufacturer's instructions and apply to the cleaned surface.
- Finishing: Once repaired, smooth the surface and consider repainting or coating to prevent corrosion.
Tools and Resources
Proper tools are necessary for effective repair:
- Welding Equipment: For welding methods, having the right welding machine and filler rods is essential.
- Adhesives: Select high-strength industrial adhesives suitable for metal bonding.
- Safety Gear: Always wear protective gear to ensure safety during the repair process.
- Guides and Manuals: Resources like Wikipedia and Britannica provide valuable insights into the metallurgy of aluminum and safe repair practices.
"Mastering the repair of cast aluminum can significantly enhance the efficiency of agricultural machinery, providing both cost savings and improved performance."
Foreword to Cast Aluminium
Cast aluminium is widely recognized for its unique properties and versatility in various applications. This section serves as an introduction to this valuable material, highlighting its significance and the indispensable role it plays in numerous industries. Understanding cast aluminium is essential for anyone interested in maintenance and repair, especially for those working in agriculture and related fields.
Definition and Properties
Cast aluminium is an alloy that undergoes a casting process, where molten metal is poured into a mold and allowed to solidify. This process enables the production of complex shapes and intricate details that are often required for industrial components.
Some key properties of cast aluminium include its lightweight nature, strength, resistance to corrosion, and good thermal conductivity. These features make this material suitable for a range of applications from structural components to artistic sculptures, providing both functionality and aesthetics. The versatility of cast aluminium is primarily due to its ability to be molded into various forms, which can lead to innovative applications.
Being familiar with these properties not only aids in the proper selection of aluminium for specific projects, but also helps in the planning of appropriate repair methods. Understanding its limitations, such as sensitivity to high temperatures and reactivity with other metals, is critical in handling cast aluminium effectively.
Common Applications
The use of cast aluminium spans across a wide array of sectors, including but not limited to:
- Automotive Industry: Cast aluminium parts are used in engine components, transmission cases, and wheels due to their lightweight and durable nature.
- Aerospace: Aircraft components often utilize cast aluminium for strength and weight savings.
- Consumer Goods: Items such as kitchen utensils and tools often leverage cast aluminium for practical and aesthetic purposes.
- Art and Sculpture: Artists use this material to create detailed structures that require both finesse and robustness.
- Construction: Components such as window frames and decorative elements capitalize on the corrosion resistance of cast aluminium.
In summary, the multifaceted utility of cast aluminium underscores its importance in various fields. Understanding its definition and applications is foundational for anyone aiming to repair or maintain cast aluminium pieces. This knowledge allows practitioners to appreciate not only the material itself but also the complexities involved in its repair and restoration.
Challenges in Repairing Cast Aluminium
Repairing cast aluminium poses significant challenges. Thiss material, while versatile and widely utilized, presents unique properties that can complicate repair efforts. Understanding these challenges is crucial for effective outcomes. The specific challenges addressed in this section include heat sensitivity, porosity and cracks, and reactivity with other metals. Each of these aspects requires careful consideration during the repair process.
Heat Sensitivity
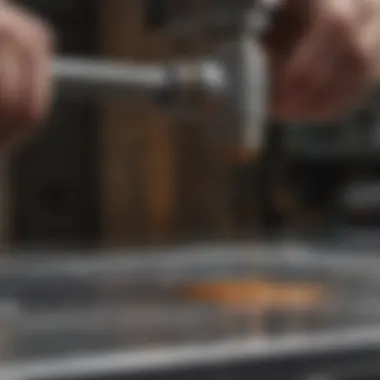
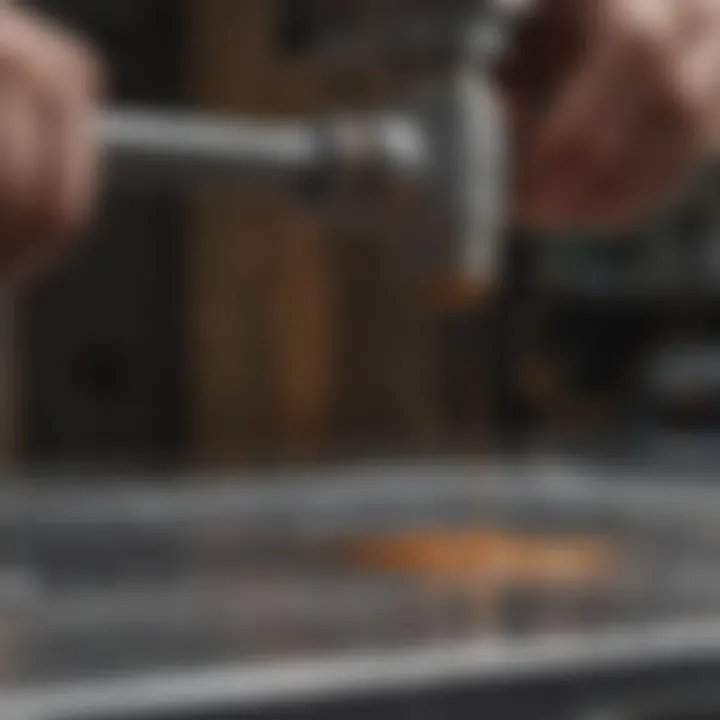
Cast aluminium is highly sensitive to heat. This property can lead to warpage and distortion when subjected to elevated temperatures during repair. It is essential to monitor the temperature closely during welding processes to avoid damaging the component. Using a cooling mechanism, such as water or air, can help in controlling heat during the welding process.
Furthermore, different grades of aluminium have varied melting points; therefore, it is critical to know the specific grade being repaired. Repair techniques must be adjusted accordingly to mitigate risk. Successful control over heat sensitivity ensures that repairs maintain the integrity of the original structure without introducing new flaws.
Porosity and Cracks
Porosity and cracks are common issues encountered in cast aluminium. Gas entrapment during the casting process can lead to voids in the material. Similarly, cracks can develop due to thermal stresses or improper handling. Porosity complicates the repair as it can weaken the repaired joint and reduce the overall strength of the component.
To address these issues, it is important to conduct a thorough examination of the area before proceeding with repairs. Non-destructive testing methods, such as ultrasonic testing, can detect subsurface defects. Filling cracks requires specific filling agents; hence, selecting appropriate filler metals that adhere well with the cast aluminium helps in reinforcing the joint.
Reactivity with Other Metals
The reactivity of aluminium, particularly with certain other metals, complicates the repair process as well. Cast aluminium reacts with metals like copper and zinc, leading to galvanic corrosion if not addressed. This reaction can significantly weaken the repaired area over time.
Thus, practitioners should be cautious when combining aluminium with dissimilar metals during repairs. Selecting compatible materials for bonding or welding minimizes such risks. For instance, using aluminium filler material when welding helps maintain material compatibility and strength in the bonded area.
In summary, understanding these challenges is vital for successful repair of cast aluminium components. Effectively addressing heat sensitivity, porosity and cracks, and the reactivity of aluminium leads to improved outcomes and lasting durability.
Pre-Repair Assessment
Effective repairs on cast aluminium start with a thorough pre-repair assessment. This process ensures that one understands the extent of damage and the specific characteristics of the material that one is dealing with. For practitioners working in fields like agriculture and horticulture, where cast aluminium parts are frequently used in equipment and tools, recognizing the initial state of the material can significantly influence the repair outcome. A proper assessment can reveal underlying issues that may not be immediately visible, thus avoiding complications later in the repair process.
Benefits of Pre-Repair Assessment
Conducting a pre-repair assessment has multiple benefits:
- Identifying Damage: Understanding whether cracks, porosity, or other issues are present is crucial.
- Planning the Repair Methodology: Knowing the specific condition can help in selecting an appropriate repair method, be it welding or adhesive bonding.
- Mitigating Future Failures: A comprehensive assessment may help identify potential weak points that could lead to future failures during use.
Assessment often involves a detailed inspection of the aluminium part. This involves observing for visible damage, checking for any signs of corrosion, and evaluating how the component fits within its intended function. Throughout this process, maintaining a keen eye for details is essential.
Visual Inspection Techniques
Visual inspection remains one of the most straightforward yet effective methods for assessing cast aluminium before repair. This technique allows one to gather immediate insights about the condition of the material without complex tools.
Key elements of visual inspection include:
- Surface Examination: Look for cracks, dents, and surface scratches. This can inform whether the part can be easily fixed or if more extensive repairs are needed.
- Joint Evaluation: If the part is welded in place, inspect the joints thoroughly. Look for incomplete fusion, undercuts, or any separation that may compromise the structural integrity.
- Corrosion Check: Understanding the presence of corrosion will guide further actions. Slight oxidization may be acceptable; however, significant pitting needs addressing.
- Comparative Analysis: If possible, compare the component with similar, intact parts to see variations in wear or damage.
Non-Destructive Testing Methods
When visual inspection is insufficient or impossible, non-destructive testing (NDT) methods provide another layer of assurance. These techniques examine the material without causing any damage, preserving its usability.
Several NDT methods can be employed:
- Ultrasonic Testing: This method utilizes sound waves to detect internal flaws. It reveals areas of weakness that are not visible on the surface.
- Dye Penetrant Testing: In this method, a colorful dye seeps into cracks, revealing their location. This is particularly useful in identifying surface-level flaws that could affect the repair process.
- Magnetic Particle Inspection: This technique is beneficial for ferrous metals but can sometimes be adapted for aluminium alloys. It helps in detecting surface and near-surface flaws.
By integrating visual inspection techniques with non-destructive testing methods, practitioners can attain a comprehensive view of the cast aluminium’s condition. This preparation paves the way for a more efficient, effective repair process and contributes to the longevity of the repaired part.
"A precise and thorough assessment is the first step toward a successful repair of cast aluminium components. Ignoring this phase can lead to expensive and time-consuming fixes later on."
Overall, the pre-repair assessment phase should not be underestimated. It lays the groundwork for informed decision-making in later repair stages.
Repair Methods for Cast Aluminium
Repair methods for cast aluminium are crucial in extending the lifespan and functionality of components made from this material. Given its widespread use in various applications, understanding these methods contributes significantly to successful repairs. Key methodologies include welding, brazing, and adhesive bonding. Each technique has its own set of considerations, advantages, and disadvantages which can impact the eventual outcome of the repair. By grasping the uniqueness of each method, practitioners can make informed decisions that enhance the durability and performance of the repaired items.
Welding Techniques
TIG Welding
TIG welding, or tungsten inert gas welding, is known for providing precise control during the welding process. This technique is essential for repairs where aesthetics and strength are paramount. One of the defining features of TIG welding is its ability to produce clean and high-quality welds, making it a popular choice for intricate cast aluminium parts. The key characteristic of using a non-consumable tungsten electrode allows for the direct melting of the material being welded, promoting a strong bond.
However, TIG welding requires a high skill level and can be time consuming. This method is particularly advantageous when working with thinner materials, offering precision that other welding methods may lack.
MIG Welding
MIG welding, or metal inert gas welding, is another prevalent technique used for cast aluminium repairs. This method is favored for its speed and the ease of operation it offers. MIG welding utilizes a continuously fed wire electrode and a shielding gas, which together facilitate an efficient welding process. Its key characteristic is the ability to weld fast, making it suitable for larger jobs where time is a constraint.
Nonetheless, MIG welding can create less refined welds compared to TIG welding. One unique feature of MIG welding is its versatility, as it can be used on various thicknesses of metals. This added flexibility can be beneficial in a workshop setting.
Stick Welding
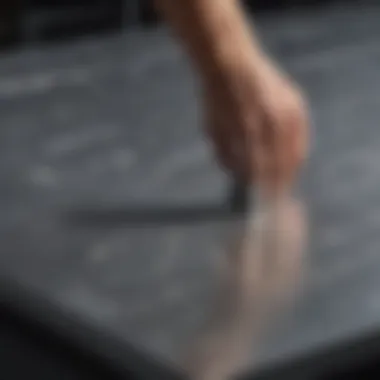
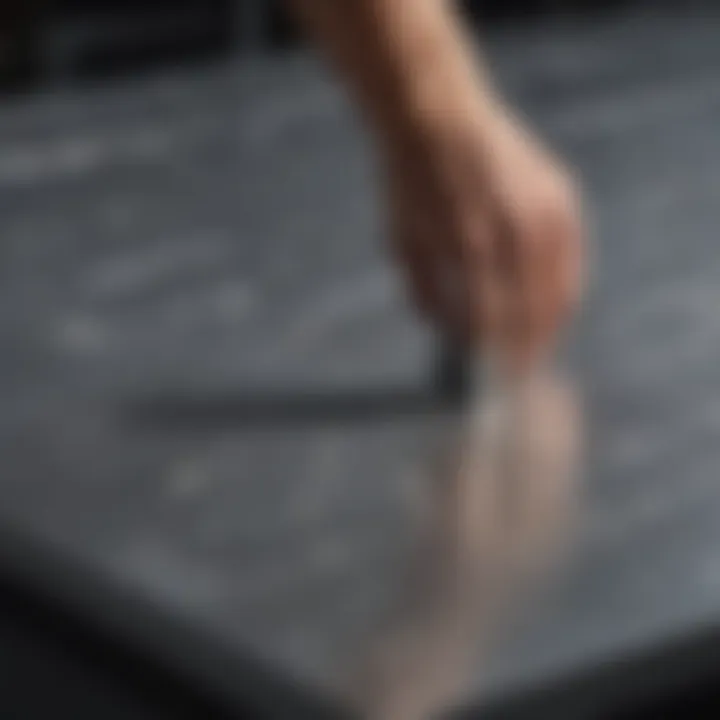
Stick welding, also known as shielded metal arc welding, is a simpler and often less expensive option for repairing cast aluminium. This approach uses a consumable electrode coated in flux, which when heated creates both the weld and a gas shield against atmospheric contamination. Its primary advantage is the equipment's portability, allowing repairs to be done in remote locations.
The key characteristic of stick welding is its usability in windy or outdoor conditions, making it practical in various environments. However, it may not provide the same precision as TIG or MIG welding. Stick welding can produce a rougher finish, which may require additional cleanup or finishing processes afterward.
Brazing and Soldering
Brazing and soldering are methods that involve using a filler material to join two pieces of cast aluminium without melting the base metals. Brazing occurs at higher temperatures than soldering and often results in a stronger joint. Typically, brazing uses materials like silver or copper alloys, requiring thorough surface preparation to ensure effective bonding.
Soldering is often used for smaller repairs and can be done with lead-based or lead-free solders. Both techniques are preferred when the integrity of the original material needs to be maintained, which can be beneficial in applications where heat distortion must be minimized. When applied correctly, these methods allow for effective repairs that preserve the material properties of cast aluminium.
Adhesive Bonding Strategies
Adhesive bonding offers a non-thermal method of repair that can be highly effective for cast aluminium. This method employs specially formulated adhesives designed to bond metals securely. Notably, epoxy and polyurethane adhesives are common choices for such applications. One significant advantage of adhesive bonding is the minimal heat input, reducing the risk of thermal distortion often associated with welding methods.
The key characteristic of adhesive bonding is its capability to transfer loads across the joint without the introduction of stress risers commonly found in welded joints. It's essential that surfaces are appropriately prepared prior to application to ensure adhesion strength. However, the curing time of adhesives can be longer, requiring planning for downtime.
Ultimately, choosing the right repair method depends on several factors including the specific application, required joint strength, and environmental considerations. Proper selection and application of these methods improve both the safety and longevity of cast aluminium structures.
Selecting the Right Repair Material
Choosing the right repair material is crucial when repairing cast aluminium. The repair material needs to match the properties of cast aluminium to ensure a durable and effective bond. Cast aluminium can be particularly sensitive, and the materials used in its repair must not compromise its structural integrity.
There are generally two main categories when it comes to selecting repair materials: filler metals and adhesives. Each of these categories presents unique characteristics and benefits that impact the outcome of the repair process.
Understanding the specific requirements of the repair job at hand is vital. Factors such as the service environment, stress levels, and the physical properties of the aluminium will influence which repair material is appropriate. For example, if the repaired component will be subject to high temperatures, selecting a filler metal with excellent heat resistance may be necessary. Meanwhile, in a situation where flexibility and ease of application are more important, an adhesive could be a better choice.
Inherent properties of the repair materials, such as corrosion resistance, bonding strength, and thermal conductivity should also be taken into consideration.
Types of Filler Metals
When repairing cast aluminium, the type of filler metal chosen significantly affects the bonding and durability of the repair. Filler metals available for cast aluminium repairs include:
- Aluminium-Silicon Alloys: Known for their excellent fluidity and low thermal expansion, these alloys are often used for welding. They maintain a good match in the expansion characteristics of cast aluminium.
- Aluminium-Zinc Alloys: These are suitable for applications that experience high-stress failures and are valued for their strong bonding when used in welding.
- Aluminium-Magnesium Alloys: They have good corrosion resistance and are ideal for repairs in marine environments, offering durability and strength.
Selecting the correct filler metal ensures that the repair withstands environmental and operational stresses.
Choosing Adhesives for Aluminium
Adhesives are increasingly used in the repair of cast aluminium, particularly in applications where welding may not be feasible. When choosing adhesives for aluminium repairs, one must consider several factors:
- Type of Adhesive: Epoxy, polyurethane, and cyanoacrylate are common types. Epoxy offers high strength and durability, while polyurethane provides flexibility.
- Surface Preparation Requirements: The condition of the aluminium surface is paramount. Proper cleaning and preparation help achieve stronger adhesion and minimize the risk of failure.
- Curing Time and Conditions: Some adhesives require specific conditions for optimal bonding. Understanding these before proceeding with repair can prevent problems later.
In sum, selecting the right repair material is not trivial. Proper material choice aligns with the application needs and enhances the repair’s effectiveness.
Remember: the success of a repair depends greatly on understanding both the material properties and the appropriate application techniques.
Post-Repair Considerations
Post-repair considerations are crucial for ensuring the longevity and functionality of cast aluminum structures. Proper attention to these aspects can prevent future issues and improve the effectiveness of the repair. After a successful restoration, it’s essential to evaluate not only the appearance but also the integrity of the material to guarantee it meets its intended use.
Surface Preparation Techniques
Surface preparation is a vital step post-repair. It serves several purposes. First, it removes any contaminants that may affect the performance of coatings and finishes applied later. Second, it helps to prepare the surface for adhesion if further bonding is necessary. Common surface preparation methods for cast aluminum include:
- Cleaning: Use solvents or biodegradable cleaners to ensure the removal of oil, grease, or dirt that might weaken future adhesion.
- Abrasive Methods: Techniques such as sanding or media blasting can enhance the surface profile, which assists in paint or coating adherence.
- Chemical Etching: This involves using acidic solutions to treat the surface, providing a better bonding capability.
These methods will not only help in achieving a better finish but also extend the life of the repair by ensuring that subsequent treatments are effective.
Finishing Processes
Finishing processes are where the functional and aesthetic aspects of the repaired cast aluminum become evident. Proper finishing can protect the material from corrosion, wear, and environmental factors. Here are primary finishing processes to consider:
- Painting: Specialized paints or coatings designed for aluminum should be used. They enhance visual appearance while delivering a layer of protection against harsh elements.
- Anodizing: This electrochemical process increases corrosion resistance and wear, making it a great choice for aluminum exposed to elements.
- Sealing: Using sealants can further protect joints or areas that have been repaired, adding an extra layer of defense against moisture and pollutants.
"Quality post-repair work directly relates to the durability of the repair, impacting overall performance in real-world applications."
By focusing on these specific techniques, owners and operators can confidently extend the lifespan of their cast aluminum components, maintaining functionality and appearance.
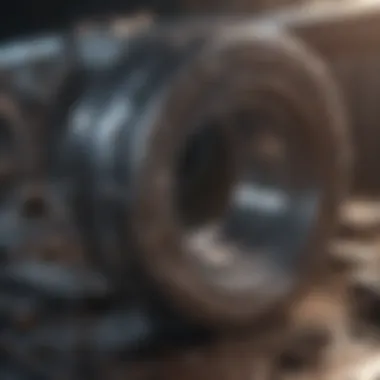
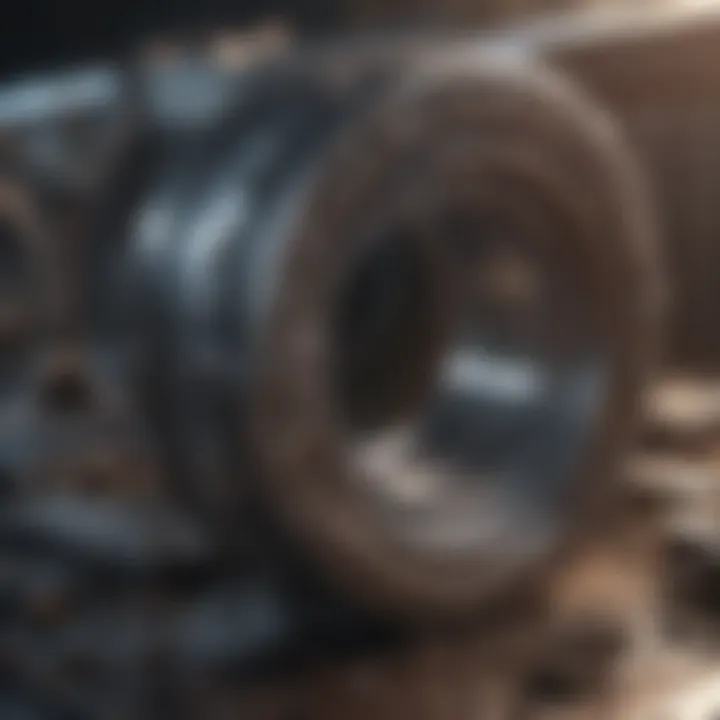
Maintenance of Repaired Cast Aluminium
Maintaining repaired cast aluminium is critical for ensuring its longevity and performance. Once a repair has been successfully executed, several factors come into play that determine the durability and functionality of the component. Regular care and understanding of the material's behavior post-repair are essential. By actively engaging in maintenance, one can prevent further damage and prolong the lifecycle of the cast aluminium pieces.
Regular Inspection Protocols
Regular inspections are foundational to effective maintenance strategies. These assessments should be systematic and thorough to identify potential issues before they escalate. Inspections can include:
- Visual Checks: Regularly visually inspecting the surface for signs of wear, corrosion, or other potential defects can reveal underlying problems.
- Measuring Cracks: Using tools to measure any cracks or gaps in the repair can assist in monitoring changes over time.
- Functional Tests: Conducting periodic functional assessments ensures the cast aluminium continues to operate as intended under various conditions.
Adopting a checklist approach can also enhance inspection consistency. Keeping detailed records of these inspections is helpful for tracking the history and condition of the material.
Preventative Measures for Longevity
Preventative measures are proactive steps to avoid future problems for repaired cast aluminium. These strategies contribute to maintaining strength and reducing the risk of wear and tear. Some important preventative measures may include:
- Proper Storage: When not in use, store cast aluminium components in controlled environments to minimize exposure to hostile conditions such as moisture or extreme temperatures.
- Protective Coatings: Applying protective coatings or sealants can shield the surface from corrosion and environmental exposure.
- Flexible Usage: Ensuring that repaired items are used within their designed limits can prevent undue stress that may lead to further damage.
Ultimately, a commitment to regular inspections and preventative measures positions one favorably to ensure that repaired cast aluminium maintains its integrity and functionality over time. Understanding these aspects is vital for anyone dealing with cast aluminium in agriculture or related fields. Regular focus on maintenance not only ensures performance but also maximizes investments made in repair.
Case Studies of Successful Repairs
Analyzing specific instances of successful cast aluminium repairs provides invaluable insights. These case studies illustrate techniques that work effectively and emphasize the nuances of choosing the right method for varying scenarios. Importantly, they demonstrate the practical application of theoretical knowledge and help avoid common mistakes. Learning from real-world examples encourages best practices and bolsters confidence in tackling repairs.
Industrial Applications
The industrial sector heavily relies on cast aluminium due to its lightweight and strength. For example, a railway company repaired a damaged cast aluminium locomotive component using TIG welding. The technician emphasized the importance of pre-heating the metal to prevent cracking, showcasing a successful approach influenced by the unique challenges of cast aluminium.
Several industries benefit from these case studies. Mining machinery often utilizes cast aluminium parts that endure significant wear and tear. In one case, a mining company successfully used brazing techniques to mend cracked aluminium components, ultimately extending the life of equipment and reducing downtime. Repair success not only saves cost but also heightens operational efficiency.
To summarize, successful repairs in industrial settings strengthen the understanding of material properties, enabling engineers to optimize not only the repair process but also the lifecycle management of their assets.
Artistic Components
Artistic and aesthetic components made from cast aluminium face different challenges. A notable case involved a sculpture artist who needed to restore an intricate cast aluminium sculpture that had suffered damage during transport. The artist chose adhesive bonding, selecting a specialized epoxy designed for metals. This method preserved the artistic integrity of the piece while ensuring a robust bond.
Moreover, studying such creative repairs illustrates a different side of cast aluminium repair. Artistic components might require a balance between durability and aesthetic quality. For instance, in another case, a restoration project of vintage furniture required careful welding techniques to not alter the original design.
These artistic cases remind us that repair techniques can extend beyond functionality. They can preserve or even enhance the original artistic vision. Each success story highlights unique aspects of working with cast aluminium, offering perspectives that resonate in both technical and creative domains.
Future Trends in Aluminium Repair Technologies
As the demand for lightweight and durable materials accelerates, cast aluminium has gained substantial traction in various sectors. Understanding the future trends in aluminium repair technologies is instrumental in realizing efficiency, performance, and sustainability. This article discusses the latest advancements poised to shape the repair landscape soon.
Advancements in Welding Technology
Welding technology is undergoing multiple advancements aimed at improving repair quality and efficiency. One significant area is the integration of automation in welding processes. Automated systems provide precise control over welding parameters, which aids in minimizing defects and enhancing the overall weld integrity.
Another notable trend is the development of new welding methods. For instance, Cold Metal Transfer (CMT) welding technology has emerged. This technology enables improved heat management, reducing the risk of distortion in cast aluminium pieces. As a result, welders can achieve high-quality joints while maintaining the original component's structural integrity.
Furthermore, training programs are increasingly focusing on advanced techniques such as TIG welding and laser welding to minimize contamination and overheating. As cast aluminium repairs become more specialized, embracing these advancements will be crucial for practitioners in various industries.
Innovations in Repair Materials
The innovation in repair materials plays a pivotal role in the efficacy of cast aluminium repairs. New materials are being developed to address specific challenges, such as porosity and thermal conductivity. For example, specialized filler metals that possess similar thermal expansion coefficients as cast aluminium are becoming available, reducing cracking risks.
Additionally, epoxy-based adhesives designed for aluminium bonding are gaining prominence. These adhesives provide strong mechanical properties and resistance to environmental factors, making them suitable for repairs in challenging conditions. They are particularly valuable for thin-walled components where traditional welding may cause damage due to heat exposure.
Various manufacturers are also exploring composite materials that blend the strengths of metals and polymers. Such materials promise to enhance repair durability while maintaining a lightweight profile.
"The integration of innovative materials can significantly alter the repair landscape, providing solutions that improve longevity and performance of cast aluminium components." - Industry Expert
In summary, the future of aluminium repair technologies hinges on advancements in welding and innovations in repair materials. These trends aim to enhance repair quality, reduce costs, and extend the service life of cast aluminium components. Employing these techniques effectively can open new avenues for practitioners, especially in agriculture and industrial applications.
Closure
The conclusion of this article encapsulates the essential insights gained throughout the discussion on repairing cast aluminium. This material, prevalent in multiple industrial and artistic applications, presents unique challenges that require specific repair methodologies. Understanding the key points discussed can optimize the approach to repairing cast aluminium, ensuring durability and functionality of the finished products.
Summary of Key Points
- Importance of Material Knowledge: Recognizing the properties of cast aluminium is crucial. Its heat sensitivity and reactivity with other metals dictate the choice of repair methods.
- Assessment Techniques: Proper visual inspections and non-destructive testing methods are fundamental. These steps highlight existing issues before repairs commence.
- Repair Methods: Various techniques exist, like welding, brazing, and adhesive bonding. Each has its own advantages, depending on the specific needs of the damage and environmental conditions.
- Material Selection: The choice of filler metals and adhesives can significantly influence the repair's success. It is vital to select materials compatible with cast aluminium.
- Post-repair Maintenance: Regular inspections and preventative strategies prolong the life of repaired components.
Final Thoughts on Cast Aluminium Repair
Repairing cast aluminium requires a thoughtful approach that combines technical knowledge and practical skills. As the discussion illustrates, the focus should not solely be on the act of repair but also on understanding the underlying properties of the material involved. With advancements in repair technologies and methodologies, practitioners can achieve successful outcomes that enhance the longevity of cast aluminium applications. Practicing these techniques not only serves immediate repair needs but fosters a culture of quality and diligence within the farming and agricultural sectors. By investing time and resources into effective repair strategies, one can contribute to sustainable practices that benefit both industry and environment.