Innovative Railcar Unloading Conveyors in Agriculture
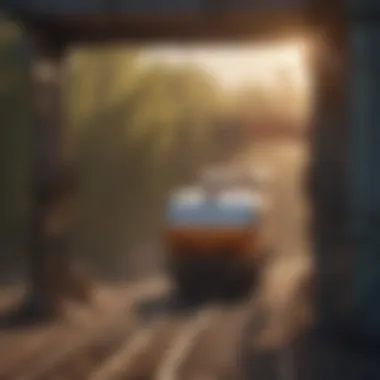
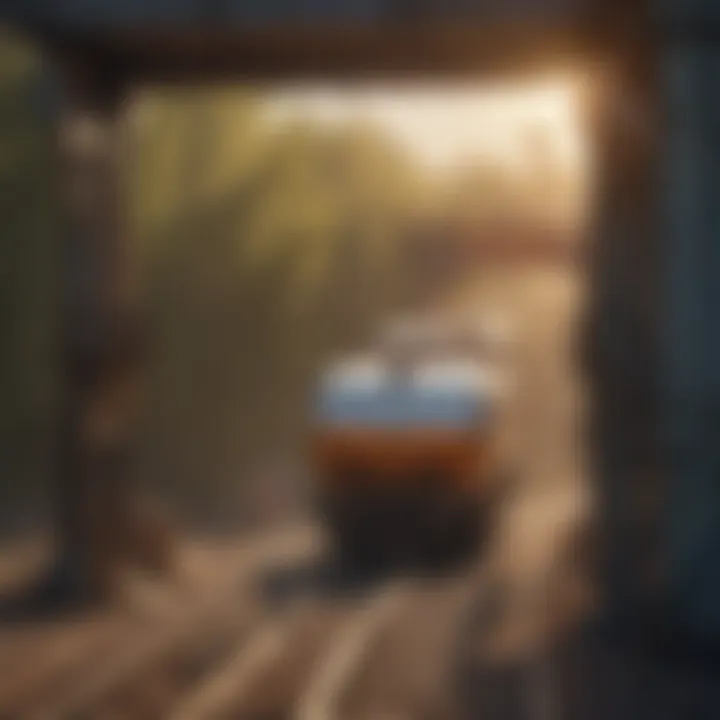
Intro
As agriculture evolves, integrating technology into operations becomes vital. Railcar unloading conveyors promise not just efficiency but a complete transformation of how commodities are handled. These systems bridge the gap between rail transport and farm operations, facilitating smoother transitions from rail to storage. Whether it's grain, fertilizer, or livestock feed, the importance of these conveyors can’t be overstated.
Understanding this technology means recognizing its components, functionalities, and applications in the agricultural landscape. With a deep dive into key concepts and recent innovations, we can uncover best practices that empower agricultural professionals to maximize productivity.
Key Concepts and Terminology
Definition of Terms
Railcar unloading conveyors basically consist of systems designed to move goods from railcars to ground-level facilities. They can be categorized by how they operate, typically as:
- Belt conveyors: Using belts to transport materials smoothly.
- Screw conveyors: Ideal for granular materials, utilizing a rotating helical screw.
- Chain conveyors: Known for their strength and durability, suitable for heavy loads.
Each type has its particular advantages, impacting speed, efficiency, and suitability for diverse commodities.
Importance in Agriculture
The role of railcar unloading conveyors is pivotal for several reasons:
- Efficiency: Reduces loading and unloading time significantly.
- Labor Reduction: Automates tasks traditionally handled by workers, freeing them for more complex agricultural roles.
- Safety: Minimizes the risk of accidents associated with manual handling.
By employing conveyors, farms can ensure that materials reach storage areas swiftly, maintaining the quality essential for agricultural success.
Current Trends and Innovations
Technological Advancements
Recent developments in railcar unloading systems harness cutting-edge technologies. Automation and robotics are becoming commonplace, allowing for real-time monitoring of material flow. For instance, advanced sensors can detect blockages, providing alerts before they become major issues. Such technological integration not only enhances operational efficiency but also contributes to predictive maintenance, thus reducing downtime.
Sustainable Practices
Sustainability is gaining traction amid concerns about environmental impact. Railcar unloading systems are incorporating eco-friendly practices. For example, energy-efficient motors and systems designed for minimal waste can reduce the carbon footprint of agricultural operations. Additionally, some companies are exploring solar energy integrations for powering these machines, making them a greener choice.
Best Practices and Techniques
Step-by-Step Guides
Implementing a successful railcar unloading system involves careful planning and execution. Here’s a simplified guide:
- Assess Needs: Determine the types of materials handled and the volume.
- Choose the Right System: Based on your assessment, select the most appropriate conveyor type.
- Install Properly: Ensure that the system aligns with existing infrastructure for maximum efficiency.
- Train Staff: Proper training is crucial to minimize mishaps and enhance productivity and safety.
Tools and Resources
To keep operations running smoothly, certain tools and resources are invaluable:
- Regular Maintenance Checks: Establish a schedule for inspections and minor repairs.
- Monitoring Software: Invest in systems that help track performance and pinpoint areas needing attention.
- Safety Gear: Equip employees with appropriate protective gear to ensure their safety during operations.
“By investing in the right technology and practices, farmers aren't just enhancing productivity; they are setting the stage for a more sustainable future.”
By delving into these aspects of railcar unloading conveyors, agriculture professionals can unlock potential that ensures both efficiency and sustainability in their operations. Beyond just moving material, these systems represent a significant step forward in modern agricultural practices.
Understanding Railcar Unloading Conveyors
Railcar unloading conveyors are an essential cog in the wheels of agricultural operations. Contemplating their impact reveals layers of efficiency, cost-effectiveness, and modernization in grain handling practices. As farmers and processors juggle the demand for speed and reliability in their operations, the understanding of railcar unloading conveyors becomes a vital part of the conversation.
Definition and Functionality
At their core, railcar unloading conveyors are systems designed to transfer bulk materials from railway cars to storage facilities or trucks. These machines come in many varieties, from belt and chain systems to pneumatic options, each serving the specific needs of the operation.
Think of it this way: when a train rolls into a loading dock filled with grain, time is money. The faster the grain can be offloaded, the quicker it can be processed or stored. This functionality isn't just about moving materials but optimizing the entire flow of operations. For instance, in larger facilities, a single delay can ripple through the supply chain, causing potential bottlenecks.
Some systems allow for automated adjustments to speed based on the type of grain being unloaded or even the environmental conditions, thus emphasizing adaptability in functionality. In essence, these conveyors turn what could be a painstakingly slow process into a streamlined operation, ensuring that every minute counts in the agricultural business.
Importance in Agricultural Supply Chain
The significance of railcar unloading conveyors in the agricultural supply chain cannot be overstated. These systems directly affect load times, labor efficiency, and, ultimately, the bottom line. To illustrate:
- Time Efficiency: Fast unloading means grains can be processed sooner, reducing storage costs.
- Reduction of Labor Costs: Automated systems decrease the need for manual labor in handling crops, enabling farmers to allocate resources more effectively.
- Quality Assurance: Smooth and gentle material handling minimizes damage to grains, ensuring that quality is preserved from railcar to storage.
"Efficient unloading can make or break the success of a harvest season, impacting everything from crop health to market pricing."
Moreover, as the market demands speed and quantity, agricultural operations that invest in modern unloading systems stand to gain a competitive edge. It's not just about keeping up—it's about staying ahead in an increasingly challenging field.
In summary, understanding railcar unloading conveyors equips agricultural professionals with the knowledge to optimize their operations, promote efficiency, and enhance performance across the supply chain. Evaluating these systems is not merely about machinery but rather about cultivating a refined approach to modern agricultural practices.
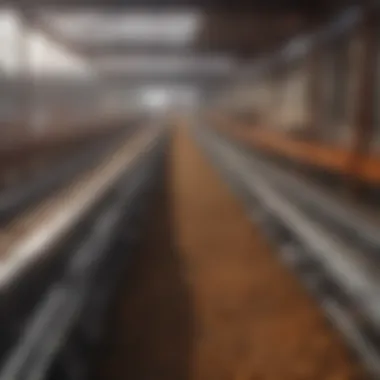
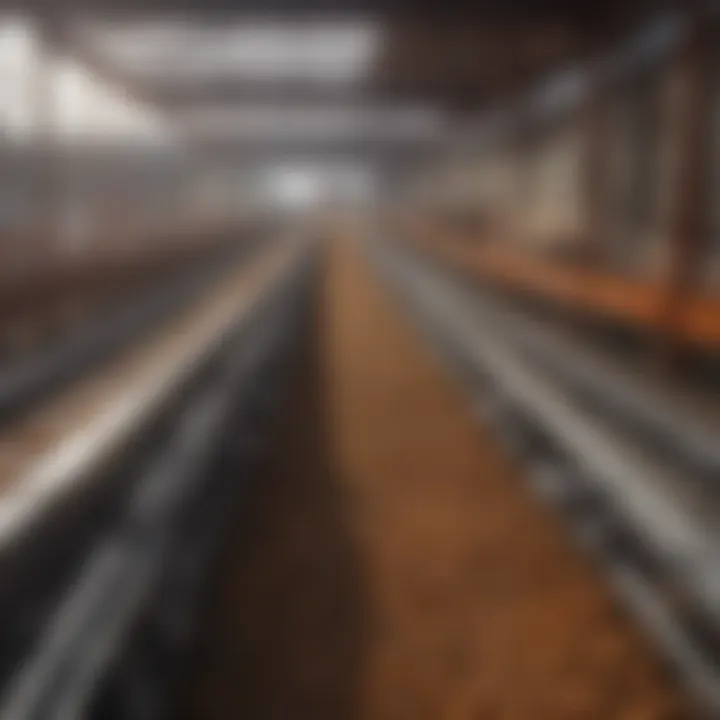
Types of Railcar Unloading Conveyors
Understanding the various types of railcar unloading conveyors is crucial for optimizing agricultural operations. Each type offers distinct advantages tailored to specific needs within the supply chain, influencing not only the efficiency of unloading but also the overall productivity of the farming process. This section explores the different types of systems, focusing on their functionalities, applications, and advantages, which ultimately contribute to more streamlined operations in grain and commodity handling.
Belt Conveyors
Belt conveyors are often viewed as the workhorses of the unloading process. They consist of continuous belts that transport materials along a pathway. One of the key benefits of using belt conveyors is their adaptability; they can handle a wide range of materials, from grains to larger agricultural commodities. Additionally, their design can be tailored to fit various loading capacities and site layouts.
The simplicity of maintenance and operation also stands out. Just a bit of routine care goes a long way when it comes to ensuring longevity. However, one thing to consider is their requirement for a flat surface. Uneven ground may necessitate additional structures, adding to the cost.
"Belt conveyors offer the ease of handling and versatility that farmers need today, but choosing the right setup can make all the difference in operational success."
Chain Conveyors
Next up, we have chain conveyors. Unlike belt systems, chain conveyors use a linked chain to move materials. These conveyors are particularly effective for heavy or dense materials, making them a go-to choice in facilities that deal with bulk commodities. The strength of chain conveyors lies in their durability; they can handle rough materials without significant wear and tear.
When comparing chain to belt, one should note the slower speed of chain systems. While this can be seen as a drawback, it allows for more control over the materials being moved, reducing the likelihood of damage to the grain or other products. The robust construction also means they can be used in harsher environments, such as areas with high humidity or dust, that might shorten the life of a belt conveyor.
Screw Conveyors
Screw conveyors are another option on the table, featuring a rotating auger that moves materials through a confined space. They are often used for unloading when space is limited. Their design allows for vertical and horizontal transport, making them quite versatile.
The effectiveness of screw conveyors is notable in handling specific materials, particularly those that are granular or powdery. They excel when transporting grains like corn and wheat, as they minimize the risk of spillage. While they may not be the quickest option available, their ability to convey materials in tighter spaces makes them a solid choice for various operations. One must also keep in mind, however, that these systems can be more complex to maintain compared to belt types.
Pneumatic Conveyors
Lastly, pneumatic conveyors introduce a different approach. This system utilizes air pressure to transport materials through tubes. More commonly observed in modern operations, pneumatic systems handle delicate materials with care, effectively minimizing breakage—a significant advantage in agricultural applications.
While their technology can be more expensive to deploy initially, the efficiency of pneumatic systems, especially in terms of speed, can pay off in the long run. They allow for multiple loading points and paths, giving farmers the flexibility necessary for diverse operational setups. On the flip side, the need for precise control over air pressure can present challenges, requiring attentive management to prevent blockages.
In summary, choosing the right type of unloading conveyor is pivotal. The varied functionalities of belt, chain, screw, and pneumatic conveyors all cater to different operational needs in agriculture. Selecting the appropriate type could very well enhance efficiency, reduce operational costs, and prevent site-related headaches.
Key Design Considerations
When delving into the intricacies of railcar unloading conveyors, the design phase stands as a critical juncture. Selecting the appropriate design features directly influences not just the efficiency of unloading but also the overall effectiveness of grain management in agricultural settings. To flourish in the competitive landscape of modern farming, a thorough understanding of key design considerations is a necessity.
Capacity and Speed Requirements
Capacity and speed requirements hinge on the volume of product being unloaded and the urgency of the task at hand. A high-throughput operation may necessitate larger, faster conveyors to keep pace with incoming railcars. If a facility typically deals with multiple railcars simultaneously, a design that can handle high capacities without faltering is indispensable. Speed, too, plays a pivotal role. An optimal speed ensures that product transfer occurs seamlessly, thus preventing downtime that can lead to significant economic losses.
Factors to consider include:
- Tonnage capacity: The specific load the conveyor must handle during peak operations.
- Speed of unloading: Ideally, this should be matched with the rate at which railcars arrive.
- Throughput efficiency: The ability to minimize delays and maximize output.
All these elements culminate in enhancing the operational rhythm. The better the design accommodates both capacity and speed, the more efficient the unloading process, ultimately bolstering productivity throughout the agricultural supply chain.
Material Compatibility
Equally important is the aspect of material compatibility. Different materials used in agricultural products have unique properties that influence their handling. For instance, sensitive grains require gentle handling to maintain quality, while heavier, more abrasive materials may necessitate stronger, reinforced conveyors. Selecting the right materials ensures the longevity of the conveyor system and mitigates any risk of damage during unloading.
Considerations in material compatibility include:
- Abrasion resistance: For materials like corn and soybeans, choose a conveyor that can withstand wear over time.
- Chemical properties: Some products may interact adversely with certain materials, necessitating careful selection.
- Temperature tolerance: Certain operations may involve hot or cold materials, requiring a suitable conveyor design for maintaining integrity under varying conditions.
Designing a conveyor that accommodates the specific materials handled aligns not only with efficiency goals but also with sustainability efforts. Using the right materials can reduce wear and tear, cut down replacement costs, and extend the lifespan of the equipment.
"Choosing the wrong conveyor might only cost a few dollars initially, but it could lead to substantial losses in productivity and quality."
In summation, addressing the nuances of capacity, speed, and material compatibility will fortify the foundation of a successful railcar unloading conveyor system. Attention to these design considerations signals an informed commitment to agricultural innovation.
Technological Advancements in Conveyor Systems
In the realm of agriculture, where efficiency can often mean the difference between profit and loss, the role of technological advancements in railcar unloading conveyors cannot be overstressed. These innovations not only enhance the operational processes but also significantly contribute to reducing labor costs and improving the accuracy of grain handling. Here, we will dissect the key technological elements that have been making waves in conveyor system design and function, ultimately benefiting agricultural professionals across the board.
Automation and Control Systems
Automation has transformed many sectors, and agriculture is no exception. The incorporation of automated control systems in railcar unloading conveyors allows for better precision, consistency, and speed in operations. For instance, modern conveyor systems now often come equipped with sensors that can detect the load levels and adjust the conveyor speed accordingly. This means there’s less chance of overloading or underfeeding, which can lead to wastage and operational inefficiencies.
Moreover, with the rise of IoT (Internet of Things), the data generated from these systems can be transmitted to centralized software for analysis. Farmers can monitor their processes in real-time from anywhere, ensuring that every grain is accounted for and handled optimally.
Integration with Agricultural Machinery
Another significant stride in conveyor technology is its seamless integration with agricultural machinery. For instance, systems are now designed to connect effortlessly with augers, seeders, or even silo machinery. This integration supports a fluid workflow, reducing the time from unloading to storage or further processing.
Benefits include:
- Reduces Downtime: The synchrony between equipment means machinery can be utilized more efficiently, leading to faster turnaround times during harvest season.
- Operational Flexibility: Farmers can adapt their processes based on daily needs, allowing for more responsive operation scaling.
- Enhanced Product Handling: Integrated systems help minimize damage to grains during transfer, maintaining quality which is essential for both storage and sale.
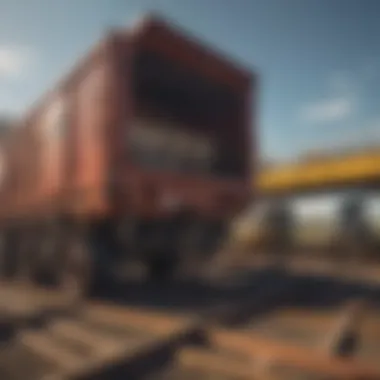
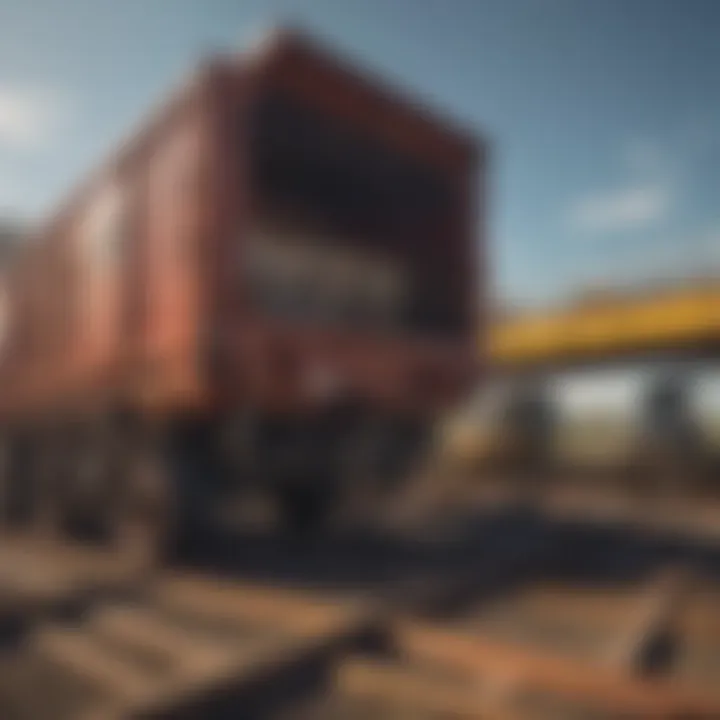
Monitoring and Diagnostic Tools
With advancements in monitoring technology, operations are no longer a guessing game. Electronic monitoring systems provide real-time feedback about various components of railcar unloading conveyors. For a farmer, this means consistently ensuring that the equipment is functioning optimally. Diagnostic tools can alert operators to mechanical issues before they escalate into full-blown failures.
The adoption of these tools can translate to:
- Predictive Maintenance: By analyzing data from diagnostic tools, maintenance can be scheduled based on actual equipment performance rather than on fixed intervals. This foresight reduces downtime significantly.
- Performance Tracking: Detailed metrics about conveyor performance can inform future investment decisions, leading to improved operational efficiency over time.
"Innovation in conveyor systems paves the way for enhanced productivity in agriculture, proving that technology and tradition can indeed go hand in hand."
In summary, technological advancements in railcar unloading conveyors serve a multitude of purposes, from enhancing automation to ensuring equipment longevity. As farmers embrace these changes, the agricultural sector can expect to see not only improved efficiency but also stronger resilience against market fluctuations and operational challenges.
Best Practices for Maintenance
Maintaining railcar unloading conveyors is crucial for their longevity and operational efficiency. Best practices for maintenance not only help in minimizing unexpected downtimes but also enhance productivity. In agriculture, where time is often of the essence, preventing breakdowns can save both money and resources. The maintenance of these systems requires a systematic approach, ensuring that every component works harmoniously.
Regular maintenance ensures that any wear and tear is identified early. This, in turn, extends the equipment's life and retains its effectiveness. Efficient operations in the agricultural sector depend heavily on the reliability of unloading systems. If your conveyor system is malfunctioning, it can lead to delays in grain handling, causing a ripple effect throughout the supply chain. Therefore, being proactive in maintenance is key to smooth agricultural operations.
Regular Inspections
Regular inspections serve as the backbone of a solid maintenance plan for railcar unloading conveyors. These inspections help to catch issues before they escalate into costly repairs. A good practice is to set up a detailed inspection schedule, focusing on the following aspects:
- Visual Checks: Look for any obvious signs of damage, such as wear on belts or chains, or misalignments in the structure.
- Lubrication Levels: Ensuring that all moving parts are well-lubricated reduces friction and wear.
- Safety Features: Verify that emergency stops and safety shields are functioning correctly.
Training personnel to conduct these inspections can build a culture of vigilance within the organization. Having a systematic checklist makes it easier and more efficient to monitor the condition of the equipment. If issues are identified early on, they can often be resolved quickly without major disruptions.
"A stitch in time saves nine."
Preventative Maintenance Techniques
When delving into preventative maintenance techniques, think of it as a form of insurance for your conveyor systems. These methods are designed to prevent malfunctions before they even happen. Here are some effective practices:
- Scheduled Maintenance: Set regular intervals for maintenance that include lubricating gears, adjusting tension in belts, and replacing worn-out components.
- Condition Monitoring: Use advanced monitoring tools to assess the health of your conveyors regularly, tracking vibrations and temperatures.
- Training Programs: Education on how to perform preventive measures goes a long way. Training staff on best practices can empower them to identify potential issues proactively.
- Documentation: Keep detailed records of maintenance activities. This data can provide insights into trends, helping to anticipate future needs and improve the decision-making process.
Preventative maintenance techniques are not just about keeping the equipment running; they also generate significant cost savings over time. The initial investment in maintenance can drastically reduce the risk of major repairs and system failures, ultimately enhancing the overall efficiency of agricultural operations.
Safety Considerations for Operation
In the world of agriculture, where machinery interacts with the elements and heavy loads, safety is paramount. Railcar unloading conveyors play a significant role in improving efficiency, but with that efficiency comes responsibility. The operation of these conveyors can present various hazards if not executed with proper safety protocols. Addressing safety considerations not only protects the workforce but also ensures the reliability of operations, reducing downtime related to accidents or equipment failures. Implementing robust safety measures fosters a culture of precaution and care, which results in increased productivity and morale in the workplace.
Operator Training and Certification
Every operation thrives on the competency of its workforce, and railcar unloading conveyors require operators who are not just trained but certified. Training encompasses everything from routine operations to emergency handling. Operators need to be well-versed in the machinery's configuration: how it works, what risks it poses, and how to mitigate those risks.
- Hands-on Experience: Practical instruction allows operators to become familiar with the equipment, creating an environment where they can learn by doing. This also builds confidence in handling complex systems.
- Understanding Regulations: Training should include familiarization with local and industry-specific safety regulations, ensuring that every operator understands compliance expectations.
- Certification Process: After completing training, a certification process can verify that an individual possesses the necessary skills. This often includes written tests and practical assessments, setting a standard for everyone operating equipment.
Without proper training and certification, even the most advanced machinery can become a hazard.
Emergency Protocols
Despite the best training and safety measures, emergencies can still arise in the field. To tackle these unforeseen challenges, clear emergency protocols need to be established.
Key Elements of Effective Emergency Protocols:
- Clear Communication: Emergency procedures should be communicated effectively to all personnel. Signage and regular drills help engrain these practices into daily routines.
- Quick Response Plans: Having a concise and clear response plan can greatly reduce recovery times. This plan should outline procedures to be followed in case of a malfunction or accident, including emergency shut-off protocols.
- First Aid Preparedness: Ensuring that first aid kits are readily available and staff are trained in basic first aid can make a significant difference in the outcome of an emergency.
"Taking precautions and being prepared for emergencies goes a long way in safeguarding our agricultural operations. It’s not just about efficiency; it’s about valuing human life and health."
The importance of having a well-structured safety operation plan cannot be overstated. Ultimately, the safety measures put in place not only enhance the overall well-being of workers but also safeguard the agricultural resources they strive to protect.
Future Trends in Unloading Solutions
In today's fast-paced agricultural landscape, the drive for efficiency and sustainability in operations is more crucial than ever. Railcar unloading conveyors, as significant cogs in the system, are adapting to meet these evolving needs. This section delves into the future trends shaping unloading solutions—particularly the growing emphasis on sustainability and data integration. Each element presents distinct advantages, enabling agricultural professionals to navigate challenges with innovative strategies that promise enhanced productivity.
Sustainability and Eco-Friendly Materials
The conversation around sustainability is gaining traction across all industries, with agriculture being no exception. Railcar unloading conveyors are increasingly incorporating eco-friendly materials and technologies. This shift is not merely about compliance but signifies a profound understanding of environmental responsibility.
Utilizing materials that minimize environmental impact isn't just good practice—it's becoming a competitive differentiator. For example, the use of recycled plastics in conveyor belts or energy-efficient motors can drastically reduce the carbon footprint of grain handling operations. Furthermore, materials that are easier to recycle promote circular economy principles that benefit both the planet and bottom line.
"Agriculture must evolve with an increasing awareness of ecological impacts on our practices and produce."
In the coming years, we can expect to see more companies providing sustainable conveyor solutions, emphasizing durability. Investing in more robust designs not only lowers replacement frequency but also lessens waste. Additionally, as farmers become more conscious of resource use, they will favor suppliers who reflect these green commitments through their products. Thus, investing in sound sustainable practices now could align with future market expectations and regulatory requirements.
Data Integration and Analytics
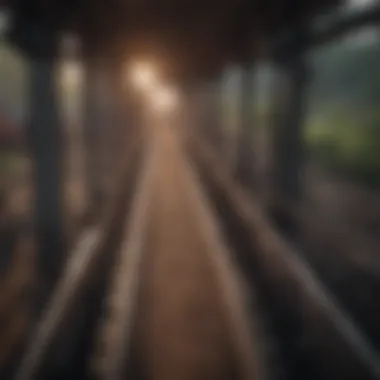
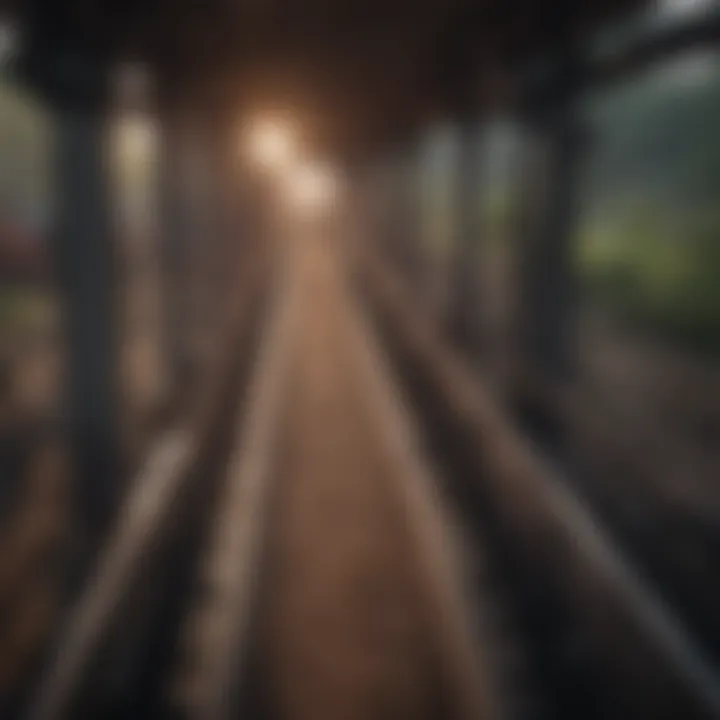
Another prominent trend is the incorporation of data analytics and integration into unloading systems. As farmers adopt smarter technologies, the gathering and wielding of data to inform decision-making are becoming quingessential.
Data analytics can optimize the performance of unloading conveyors, where metrics such as conveyor speed and throughput are continuously analyzed. By utilizing real-time monitoring systems, operators can adjust strategies based on current conditions, ultimately leading to more responsive and effective operations.
Moreover, integrating conveyor systems with existing agricultural machinery can create a seamless data-sharing network. For instance, by combining information from railcar unloading conveyors and grain silos, farmers can develop a comprehensive understanding of their supply chain dynamics. This approach not only streamlines operations but fosters an environment where informed decisions lead to improved yield and resource management.
In summation, the future of unloading solutions is poised to embrace sustainability alongside data-driven strategies. With these advancements, the agricultural sector stands to gain in efficiency, reduced waste, and a more profound connection to both the market and the environment.
Case Studies in Innovative Implementations
Examining real-world applications of railcar unloading conveyors reveals a treasure trove of insights for agricultural practitioners. These case studies illustrate not only successful implementations but also the hurdles that have been encountered and overcome. Identifying specific scenarios helps to understand the effectiveness of different conveyor systems in unique agricultural setups.
Successful Operations
One notable instance is the deployment of a modular belt conveyor system at a grain storage facility in the Midwest. This facility was struggling with slow unloading times, causing delays in their logistics pathway. By installing this conveyor, they increased their unloading capacity significantly. Within weeks of the installation, they observed an improvement of 30% in unloading speed.
- Efficiency Gains: The facility could process more grain in less time, allowing it to handle higher volumes during peak harvest season.
- Reduced Labor Costs: With the automated system in place, reliance on manual labor decreased, resulting in lower overtime costs during harvest time.
- Flexibility: The modular design allowed easy adjustments to adapt to different types of railcars or commodities being unloaded.
Such case studies bring to light the tangible benefits of modern conveyor systems in enhancing operational efficiency. They also help create a benchmark against which other agricultural operations can measure their performance and identify areas for improvement.
Challenges and Solutions
However, the journey towards successful implementation isn’t without its bumps in the road. In another case, a farm located in the Southwest faced significant issues with the integration of a screw conveyor. While the conveyor was expected to streamline grain unloading, several problems arose during the initial phase.
Challenges Faced:
- Clogging Issues: The materials being conveyed had a tendency to pack tightly, leading to clogged systems.
- Maintenance Disruptions: Unforeseen mechanical failures caused sporadic downtime, which jeopardized agricultural schedules.
- Initial Training Gaps: Operators struggled with the control systems, not fully grasping the functionalities.
To address these issues, the farm implemented thoughtful solutions:
- Material Inspection: They chose to audit the material properties before unloading, ensuring compatibility with the screw conveyor system.
- Scheduled Maintenance: Regular checks were instituted, which minimized disruptions and provided insights into potential wear and tear.
- Comprehensive Training: They invested time in operator training sessions, focusing on troubleshooting and efficient use of the system.
These adjustments not only salvaged the screw conveyor’s implementation but also provided the team with valuable lessons that could be beneficial in similar future projects. Ultimately, the importance of adapting to challenges during the introduction of new technologies cannot be overstated, as overcoming them can lead to innovative practices that shape future operations in agricultural settings.
"The path to innovation is often paved with unexpected trials; however, those who persist reaps the rewards of improvement and efficiency."
Through the lens of these case studies, it becomes clear how railcar unloading conveyors can drastically alter and enhance agricultural productivity. The shared experiences reflect a collective learning journey, offering invaluable insights that can help others thrive in their own endeavors.
Economic Impact of Railcar Unloading Conveyors
The inclusion of railcar unloading conveyors in agriculture isn't merely a matter of operational efficiency; it has significant financial ramifications as well. These systems can significantly influence profitability, competitive advantage, and overall economic viability in agricultural operations. From optimizing labor costs to enhancing throughput, the economic impact of these conveyors is profound and multi-faceted.
Cost-Benefit Analysis
The cost-benefit analysis of railcar unloading conveyors serves as an invaluable tool for agricultural managers looking to make informed decisions. Simply put, it involves weighing the costs of acquisition and maintenance against the expected benefits from improved efficiency and productivity.
Key Considerations:
- Initial Investment: The upfront cost of these conveyors can be substantial, encompassing not just the purchase price but also installation, training, and any necessary adaptations to existing systems. However, it's essential to frame this cost in terms of its potential return.
- Operational Efficiency: Improved unloading times can lead to higher throughput during critical harvest periods, effectively increasing the bottom line. A system that can unload railcars quicker minimizes downtime and maximizes productivity.
- Maintenance Costs: While these systems require upkeep, advanced models often come with features that reduce the need for frequent repairs. Evaluating these potential savings over time is crucial.
- Labor Savings: By automating the unloading process, farms can significantly reduce the labor required for this activity, allowing personnel to focus on other value-added tasks. The reduction in labor costs is often one of the more compelling arguments in favor of these conveyors.
Return on Investment
When considering any capital investment, especially one as pivotal as railcar unloading conveyors, understanding the return on investment (ROI) is essential. This concept goes beyond just the immediate payback period; it encompasses the long-term gains and strategic advantages that these systems may afford.
Factors Influencing ROI:
- Increased Throughput: Conveyors allow for faster unloading, equating to higher volumes processed daily. This can be particularly beneficial during peak seasons when every minute counts.
- Reduced Downtime: Efficient unloading means less time spent waiting for trucks to arrive, thus keeping other machinery busy and contributing to a more streamlined operation overall.
- Market Competitiveness: The ability to handle shipments quicker and with less labor enables farms to compete more effectively in a dynamic market. In essence, it positions them as more reliable suppliers.
- Adaptability to Scale: As operations grow, investment in conveyors can scale with increased production and shipment capacities without a corresponding spike in unforeseen costs.
In essence, while the initial outlay for railcar unloading conveyors might seem daunting, the prospects for ROI are promising. These conveyors not only enhance the immediate efficiency of agricultural processes but also help farmers capitalize on longer-term trends and market demands, making them an investment worth serious consideration.
"Investing in railcar unloading systems is not just a matter of efficiency—it's an investment in future-proofing agricultural operations."
Ultimately, analyzing the economic impact of railcar unloading conveyors through the lenses of cost-benefit analysis and ROI provides a well-rounded understanding of their critical role in the agriculture supply chain.
Epilogue
The significance of railcar unloading conveyors in agricultural practices cannot be overstated. These systems are the backbone of efficiency when it comes to the movement of grains and commodities from railcars to storage facilities or processing plants. Their role extends beyond basic functionality, touching on aspects such as productivity, safety, and economic viability. As we draw our analysis to a close, it’s essential to recap the various aspects that stand out in utilizing these conveyors effectively.
Summarizing Key Insights
To summarize, railcar unloading conveyors are not just mechanical systems; they represent a crucial innovation in the agricultural supply chain. Some key insights from this article include:
- Diverse Options: Different conveyor types, like belt, chain, and pneumatic, serve varied needs, making it essential for farmers to choose based on their specific requirements.
- Technological Integration: Modern systems integrate cutting-edge automation and control technologies, enhancing operational efficiency and safety.
- Maintenance Matters: Regular inspections and preventive maintenance save costs and ensure machinery longevity. Addressing wear and tear proactively is not just a best practice; it’s a lifeline for sustaining operations.
- Safety Protocols: Sound operator training and emergency protocols are vital aspects that can never be overlooked. Human error is a risk factor, and prepared operators help mitigate associated dangers.
- Economic Advantages: The economic impact of these conveyors can be profound. Through improved handling speed and reduced labor costs, farmers are likely to see a beneficial return on their investment.
"The right conveyor system can change the game, enabling operations that directly affect harvests and ultimately, profits."
Future Perspectives
As the agricultural landscape continues to evolve, so too do the expectations from unloading systems. Looking ahead, we can easily identify trends that will shape future developments:
- Sustainability Focus: With growing awareness about environmental impacts, more manufacturers are exploring sustainable materials and practices, making eco-friendly conveyor systems a priority.
- Data-Driven Decisions: As data analytics becomes more accessible, farmers will leverage insights from their operations, tweaking processes for even higher efficiencies. Robust monitoring systems will aid in making informed adjustments based on real-time data.
- Enhanced Automation: The move towards greater automation will likely continue, with systems becoming more autonomous, needing less human intervention. This trend can help streamline operations but also demands that operators remain knowledgeable about these technologies.
In closing, understanding railcar unloading conveyors is key for agricultural professionals aiming to improve their operations. The conversation doesn’t stop here; it is an ongoing journey of innovation and adaptation.