Hatchery Machines: Understanding Their Role in Agriculture
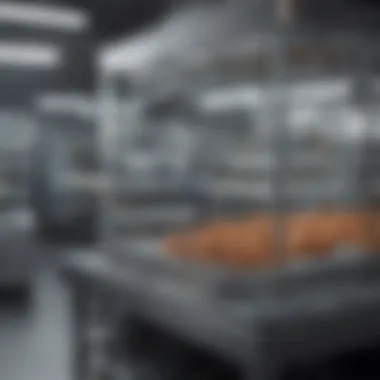
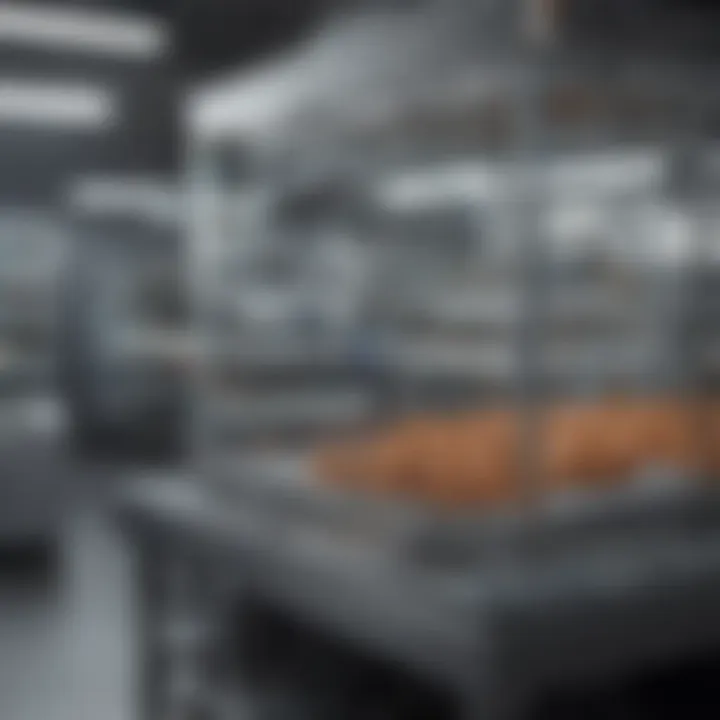
Intro
In the evolving landscape of agriculture, hatchery machines play a critical role in enhancing the efficiency of poultry farming. Their technology is designed to optimize the incubation of eggs, ensuring a higher yield of healthy chicks. As farmers strive to adopt sustainable methods, understanding these machines becomes essential. This section introduces key concepts and terminology related to hatchery machines, setting a foundation for the subsequent discussion.
Key Concepts and Terminology
Definition of Terms
Hatchery machines refer to the equipment used for incubating and hatching eggs in a controlled environment. They maintain specific conditions such as temperature, humidity, and ventilation. Understanding the following terms provides clarity:
- Incubation: The process of maintaining eggs under controlled conditions to support embryo development.
- Fertility Rate: The percentage of eggs that result in live chicks after hatching.
- Hatchability: The proportion of eggs that successfully hatch into chicks.
Importance in Agriculture
The significance of hatchery machines cannot be understated. They not only improve hatchability but also address food security by contributing to a steady supply of poultry. By using these machines, farmers can rely on data-driven insights, thereby enhancing their production methods. The integration of hatchery machines aligns with modern agricultural practices, promoting efficiency and sustainability in poultry farming.
Current Trends and Innovations
Technological Advancements
Modern hatchery machines incorporate advanced technology, such as computerized control systems that allow for precise regulation of incubation parameters. Features like automated egg turning and real-time monitoring improve outcomes significantly. These innovations aim to minimize human error and enhance livestock welfare.
Sustainable Practices
Sustainability is increasingly becoming a focus in agricultural practices. Hatchery machines support this trend by enhancing energy efficiency. Some machines now use renewable energy sources, thereby reducing the carbon footprint of poultry production. Additionally, the application of environmentally friendly materials in machine construction reduces waste.
Best Practices and Techniques
Step-by-Step Guides
For successful incubation and hatching, following best practices is vital:
- Pre-Setup: Ensure that the hatchery machine is clean and calibrated for optimal performance.
- Egg Selection: Choose eggs that are fertile and free from damage.
- Monitoring: Regularly check temperature and humidity levels throughout the incubation period.
- Post-Hatching Care: Provide adequate resources for the chicks immediately after hatching to promote health and growth.
Tools and Resources
Farmers can benefit from various tools and resources:
- Incubator Monitoring Systems: Keep track of incubator conditions.
- Poultry Farming Forums: Engage with other farmers to share experiences and insights.
- Educational Materials: Invest in courses or online resources to deepen understanding of hatchery operations.
"The advancement of hatchery machines not only revolutionizes poultry farming but promotes a more sustainable future for agriculture."
Understanding hatchery machines is essential for any farmer aiming to improve efficiency and productivity in poultry farming. By grasping the key concepts and keeping up with current trends and best practices, farmers can effectively leverage these machines to boost their operations.
Understanding Hatchery Machines
Hatchery machines play a crucial role in modern poultry farming. Their significance lies in the precise control they offer over incubation conditions. This ensures that the eggs receive optimal care, which is vital for hatching healthy chicks. Farmers must understand how these machines operate to maximize their productivity and sustainability.
Definition and Purpose
A hatchery machine, simply put, is an apparatus used to incubate eggs until they hatch. These machines are designed to create an environment that mirrors natural conditions. The temperature, humidity, and airflow are controlled to optimize the chances of successful hatching. The primary purpose is to improve hatch rates, reduce the risk of disease, and enable a uniform development of the embryos.
In essence, hatchery machines eliminate many of the uncertainties associated with natural incubation. They allow producers to hatch chicks on a larger scale while maintaining high standards of quality and efficiency. For instance, a commercial hatchery can significantly increase its productivity by utilizing advanced incubation technology.
Historical Development
The evolution of hatchery machines reflects advancements in agricultural practices. Early methods relied on simple, passive warming techniques. An incubator could be as basic as a wooden box lined with straw, relying on external heat sources. Over the years, several innovations transformed these rudimentary systems.
In the late 19th century, the introduction of mechanical devices that regulated temperature marked a turning point. These developments made it possible to achieve consistent conditions, which was previously challenging. The 20th century brought significant changes with the invention of forced air incubators. These machines enhanced airflow and further regulated the environment.
Today, modern hatchery machines incorporate smart technology. These advancements allow remote monitoring and adjustments, optimally balancing environmental factors. As breeding conditions continue to improve, understanding the historical context of hatchery machines helps appreciate their current capabilities and future potential.
Types of Hatchery Machines
Understanding the various types of hatchery machines is crucial for anyone involved in poultry farming or related agriculture. Each machine type offers distinct functionalities that can affect incubation processes, hatch rates, and overall farm efficiency. When selecting a hatchery machine, farmers must carefully evaluate their needs, budget, and the specific requirements of the eggs being incubated. Here, we will explore four primary types of hatchery machines, each with unique characteristics and advantages.
Centrifugal Hatchery Machines
Centrifugal hatchery machines utilize centrifugal force to create an environment that circulates air and maintains consistent temperature and humidity levels. This technology ensures an even distribution of warming air, which is essential for proper embryo development. The design minimizes dead zones where eggs might not receive adequate warmth, leading to higher hatch rates.
A key advantage of centrifugal machines is their capacity for large-scale operations. Farms that manage hundreds or thousands of eggs can particularly benefit from this efficiency. However, users must consider the initial investment as these machines can be more costly compared to simpler models.
Forced Air Incubators
Forced air incubators are popular in both small- and large-scale operations. These machines use fans to circulate heated air around the eggs, ensuring uniform distribution of warmth. The presence of forced air reduces the risk of hot or cold spots, which can negatively affect hatch success.
These incubators are particularly advantageous in their versatility; they can adapt to various egg types, making them suitable for a range of poultry species. Furthermore, forced air incubators allow for easy monitoring of temperature and humidity through integrated controls. The slight drawback may be the need for more frequent maintenance to keep fans operating optimally.
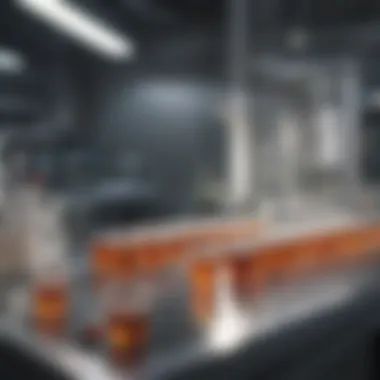
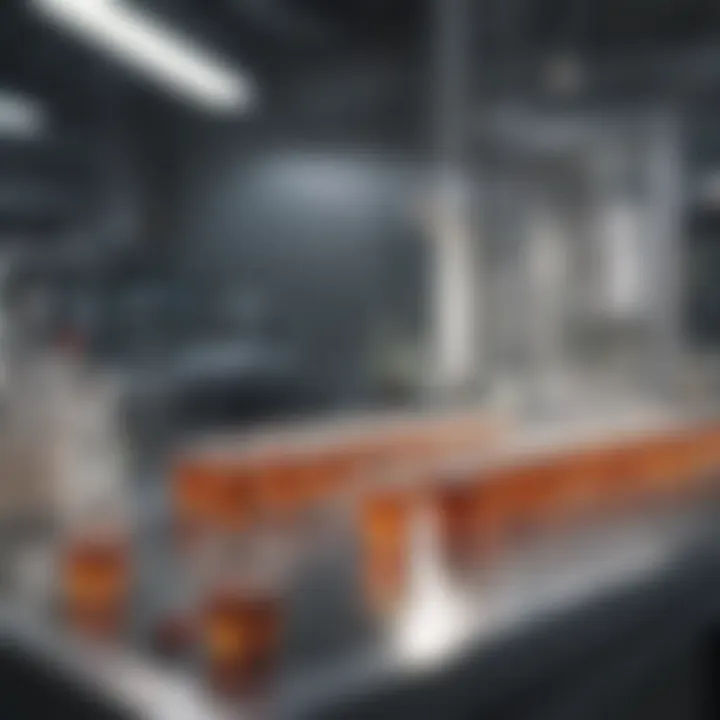
Still Air Incubators
Still air incubators are a simpler option that does not use fans for air circulation. Instead, they rely on natural convection currents. This can lead to some challenges in maintaining consistent temperature, as cooler air can settle at the bottom of the incubator.
However, still air incubators are less expensive and easier to operate, making them a good choice for beginners or small farms. These machines are often used for hatching chickens and other smaller poultry types. While they may not provide the same level of consistency as forced air incubators, they can still produce satisfactory results if managed carefully.
Advanced Digital Machines
Advanced digital hatchery machines incorporate cutting-edge technology, offering features like digital displays and automated control systems. These machines can monitor and adjust temperature, humidity, and airflow in real-time, ensuring optimal conditions for embryo development.
The integration of IoT (Internet of Things) allows for remote monitoring, which can be extremely beneficial for farmers managing multiple hatcheries. With such technology, farmers can receive alerts and data metrics, making it easier to maintain optimal incubation conditions. The trade-off here is often higher costs, but the investment can lead to increased hatch rates and operational efficiencies, making them attractive for progressive poultry operations.
Core Mechanisms of Hatchery Machines
The efficiency of hatchery machines hinges on their core mechanisms. These systems are crucial in simulating the natural conditions that eggs require for successful incubation. By understanding these mechanisms, one can appreciate the technology’s role in optimizing hatch rates and ensuring the health of the embryos. Each aspect—temperature control, humidity regulation, and airflow management—plays a vital role in this process.
Temperature Control Systems
Temperature control is fundamental to the incubation process. Eggs have a specific temperature range in which they develop optimally, usually around 99 to 102 degrees Fahrenheit. If the temperature falls outside this range, it can lead to significant negative outcomes like embryo mortality or poor growth post-hatching. Modern hatchery machines are equipped with advanced thermostats and sensors that continuously monitor and adjust the temperature.
The ability to maintain a stable temperature is not just about hitting a number on a screen. It is about creating an environment where the embryos can thrive. For example, digital incubators often feature precise controllers that allow operators to set desired temperatures. Furthermore, some machines can automatically compensate for external temperature changes, ensuring that the internal environment remains stable.
"Temperature fluctuations can lead to inconsistencies in hatch outcomes and can significantly affect the overall productivity of the hatchery."
Humidity Regulation
Humidity is another critical factor influencing the successful incubation of eggs. Eggs require a specific level of moisture in the air to ensure proper embryo development and hydration. If humidity is too low, it can result in dehydration, while excessive humidity can lead to bacteria growth and contamination.
Hatchery machines incorporate humidifying systems to maintain optimal humidity levels, often ranging from 45% to 55% relative humidity, depending on the species of egg being incubated. Incorporating hygrometers into machines helps in monitoring these levels continuously.
Effective humidity regulation also impacts the metabolic processes within the egg. As such, many modern hatchery machines come with integrated systems that adjust humidity levels based on real-time data. The balance between humidity and temperature is crucial for achieving the best hatch rates.
Airflow Management
Airflow management is essential for ensuring that embryos receive adequate oxygen. Inadequate oxygen levels can impede growth and lead to malformed chicks. Hatchery machines are designed to ensure adequate ventilation without creating drafts that can disturb the temperature and humidity levels.
Many advanced machines use fans that circulate air around the eggs evenly. This circulation aids in distributing heat and humidity homogeneously throughout the incubator. Proper airflow also helps in removing carbon dioxide produced by the developing embryos.
In summary, the core mechanisms of hatchery machines—temperature control systems, humidity regulation, and airflow management—work in unity to create an optimal environment for egg incubation. By mastering these mechanisms, hatchery operators can significantly enhance their productivity and ensure healthier outcomes.
Advantages of Using Hatchery Machines
Hatchery machines offer numerous benefits to poultry farming. They play an essential role in streamlining the incubation process, improving the outcomes for hatcheries, and subsequently enhancing overall productivity. Understanding these advantages can reveal their importance in modern agricultural practices, especially as the demand for sustainable farming continues to grow.
Increased Hatch Rates
One primary advantage of using hatchery machines is their capacity to significantly increase hatch rates. Hatch rates refer to the percentage of viable eggs that successfully hatch into chicks. Traditional incubation methods can be unpredictable and often result in lower hatch rates due to varying environmental conditions. Hatchery machines provide controlled climates that maintain optimal temperature and humidity levels. This regulated environment minimizes the risks of failures associated with manual incubation. Many advanced machines now come equipped with digital monitoring systems that alert users to fluctuations that can compromise egg viability.
Research indicates that hatchery machines can elevate hatch rates by 10% to 20% compared to traditional methods. These improvements directly impact the profitability of poultry operations, allowing farmers to maximize their yield from every batch of eggs.
Labor Efficiency
Another key advantage of hatchery machines is their impact on labor efficiency. Manual incubation processes are labor-intensive and require constant monitoring. By adopting modern hatchery machines, farmers can reduce the workload on staff. With automated features like egg turning, temperature adjustments, and humidity regulation, machines handle many tasks that previously required attention.
Reduced labor not only cuts down costs but also allows workers to focus on other essential activities within the farm. For instance, personnel can shift their efforts to health management, feeding, and other vital aspects of poultry care. Consequently, this leads to an uptick in the overall efficiency and productivity of the farm.
Consistency in Results
Hatchery machines ensure a level of consistency in the hatching process that is often unattainable in natural or traditional methods. Each cycle in a hatchery machine can be precisely calibrated, offering predictable results that are crucial for farmers. Consistency is a significant factor in meeting market demands, as unpredictable hatch rates can lead to supply chain issues.
Using hatchery machines means that businesses can forecast production more accurately. Advanced models often log data on each incubation cycle, allowing farmers to analyze trends and make adjustments as needed. Ultimately, this data-driven approach to incubation forms a solid foundation for making strategic business decisions, leading to sustainable growth.
"The integration of hatchery machines not only optimizes the incubation process, but it also creates a more efficient agricultural system that can meet the world's growing food demands effectively."
In summary, the advantages of using hatchery machines encompass increased hatch rates, improved labor efficiency, and consistent results. These strengths make them invaluable in the current landscape of poultry farming, driving forward efficiency while supporting sustainable agricultural practices.
Challenges in Hatchery Machine Usage
The deployment of hatchery machines brings numerous benifits, but it is not without its challenges. These challenges can significantly affect operational efficiency and profitability in poultry farming. Understanding these obstacles is crucial for farmers and stakeholders who want to maximize the advantages that these machines offer.
High Initial Investment Costs
Acquiring hatchery machines involves a considerable financial commitment. The cost varies significantly based on the type and sophistication of the machine. For example, advanced digital machines and automated systems often have higher price tags compared to simpler still air incubators. Farmers must evaluate whether the expected increase in hatch rates and labor efficiency justifies the initial outlay.
Benefits and Considerations:
- ROI Assessment: Farmers should conduct thorough analyses to determine the return on investment. Over time, higher hatch rates can lead to more chicks, which may offset the initial costs.
- Financing Options: Various programs exist to support farmers in financing these investments, which can help ease the burden of high upfront costs.
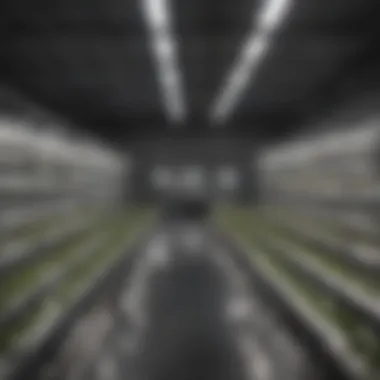
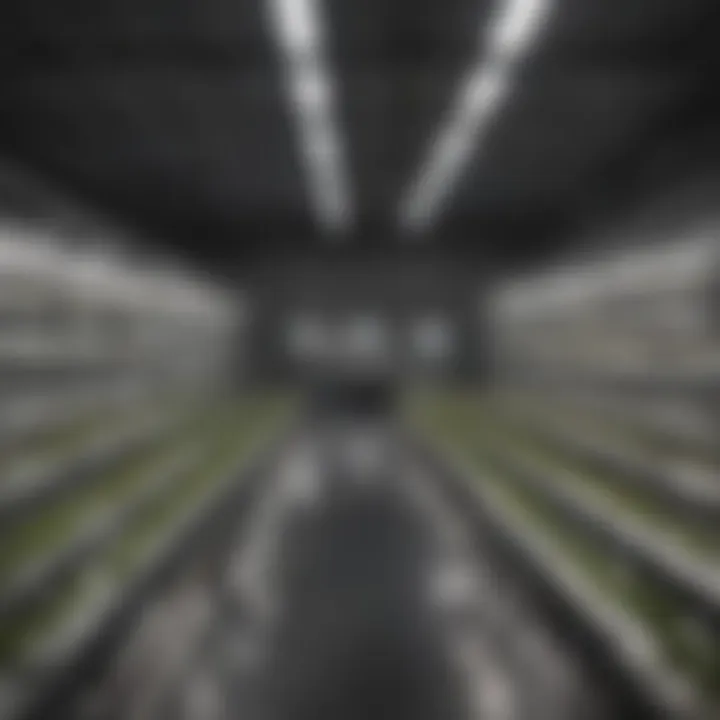
Technical Failures and Maintenance
Another concern is the potential for technical failures in hatchery machines. These disruptions can result in lost batches of eggs, detrimentally affecting hatch rates and overall business viability. Regular maintenance is vital to ensure optimal performance.
Maintenance Recommendations:
- Scheduled Inspections: Regular check-ups can identify issues before they escalate.
- User Training: Proper training for operators helps in the keen understanding of the machinery. Familiarity reduces the chances of mishandling or operational errors.
Common Failures:
- Temperature Fluctuations: Inconsistent temperature can compromise embryo development.
- Humidity Control Issues: Similar to temperature, humidity levels must remain stable for successful hatching.
Environmental Impact Considerations
With the growing emphasis on sustainability in agriculture, the environmental impact of hatchery machines cannot be overlooked. These machines consume energy and may produce waste that can affect the local ecosystem.
Key Focus Areas:
- Energy Efficiency: Investing in energy-efficient models can minimize the carbon footprint, contributing to more sustainable practices.
- Waste Management: Implementing proper waste disposal methods is necessary to mitigate potential environmental harm.
"Sustainability is not just an option; it's a prerequisite for the future of agriculture."
Technological Advancements in Hatchery Machines
Technological advancements have substantially shifted the landscape of hatchery practices, impacting efficiency, productivity, and sustainability. This section looks at vital innovations that have emerged in hatchery machines. As the agriculture sector moves towards more integrated and efficient methods, the role of technology becomes increasingly important. Automation and smart technology, alongside the integration of Internet of Things (IoT), pushed the boundaries of traditional practices, optimizing the entire incubation process.
Automation and Smart Technology
Automation in hatchery machines aims to reduce manual labor and improve turkey hatchery workflow. Automation systems streamline the monitoring of temperature, humidity, and airflow without requiring constant human intervention. These machines can adjust settings in real-time, resulting in improved hatch rates and overall success.
Benefits of automation include:
- Consistency: Automated systems carry out tasks precisely, making it easier to achieve optimal conditions for hatching.
- Labor Reduction: By minimizing manual checks and adjustments, farmers can allocate resources to other vital areas, enhancing productivity.
- Data Collection: Many automated machines come equipped with data collection capabilities, enabling farmers to analyze performance metrics and refine their processes.
Incorporating smart technology adds another layer of sophistication. Machines may be equipped with sensors that monitor environmental variables continuously. The data from these sensors can be accessed via smartphones or computers, allowing producers to make informed decisions, even from a distance. This enhances not only the efficiency of operations but also supports proactive management of hatchery conditions.
Integration of IoT in Hatcheries
The integration of IoT in hatcheries signifies a shift towards data-driven agriculture. IoT technology allows hatchery machines to communicate with other devices and systems, creating a network of interconnected equipment. This connectivity fosters better decision-making and improved operational effectiveness.
Key aspects include:
- Remote Monitoring: Farmers can observe environmental conditions in real-time, enabling immediate adjustments when necessary to prevent failures in incubation.
- Predictive Maintenance: IoT devices often can predict when a machine requires maintenance or repair, thus reducing downtime and enhancing reliability.
- Enhanced Efficiency: By optimizing the entire ecosystem of a hatchery, producers achieve higher productivity levels.
"The future of hatcheries is not just about producing more but doing so sustainably and efficiently."
By embracing these innovations, farmers can ensure their operations are not only viable but thriving, contributing positively to the overall agricultural ecosystem.
Maintenance and Care for Hatchery Machines
Proper maintenance and care for hatchery machines is crucial in ensuring their functionality and longevity. Regular upkeep can significantly impact hatch rates and the overall health of the incubated eggs. Ensuring that machines operate at optimal efficiency prevents technical failures and enhances productivity in hatcheries. In addition, this aspect directly influences operational costs and fosters sustainable practices in poultry farming.
Regular Cleaning Protocols
Cleaning protocols for hatchery machines should not be overlooked. Contamination can lead to disease outbreaks, affecting hatchling survival rates. Regular cleaning helps remove debris, dust, and bacteria that accumulate during the incubation period.
- Daily cleaning should include wiping down surfaces and checking filters for dust accumulation.
- Weekly cleaning might consist of a more thorough cleaning, including disinfecting surfaces with approved veterinary cleaners.
- It is prudent to establish a monthly deep cleaning schedule to ensure all areas are addressed, removing any hard-to-reach dirt.
By keeping the machines clean, hatcheries can minimize health risks associated with poor sanitation.
Calibrating Temperature and Humidity Controls
Calibrating temperature and humidity controls is essential for maintaining optimal incubation conditions. Fluctuations in these parameters can lead to decreased hatchability and unhealthy chicks. A robust calibration routine helps in achieving consistency.
- Temperature Settings: Regular checks should be performed to ensure temperatures align with species-specific requirements. Digital machines often include calibration guides.
- Humidity Levels: Monitoring humidity levels is critical. Using hygrometers can help verify readings and facilitate necessary adjustments. Maintaining the right humidity will ensure proper embryo development.
- Documentation: Keeping detailed records of calibration checks can help identify trends, enabling proactive adjustments.
Routine Inspection and Repairs
Routine inspections and timely repairs can greatly enhance machine lifespan. Regular inspections can catch potential problems before they escalate into costly failures.
- Weekly Inspections: Checking for any signs of wear or malfunction, including fan function and seal integrity, is advisable.
- Replacement Parts: Having a ready supply of common replacement parts can minimize downtime.
- Professional Servicing: Consider arranging for periodic professional service. Experts can identify issues that may not be visible during routine checks.
"Regular maintenance is not just about cleanliness; it is about ensuring that each machine functions to its full potential."
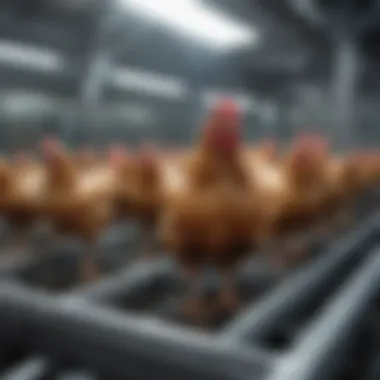
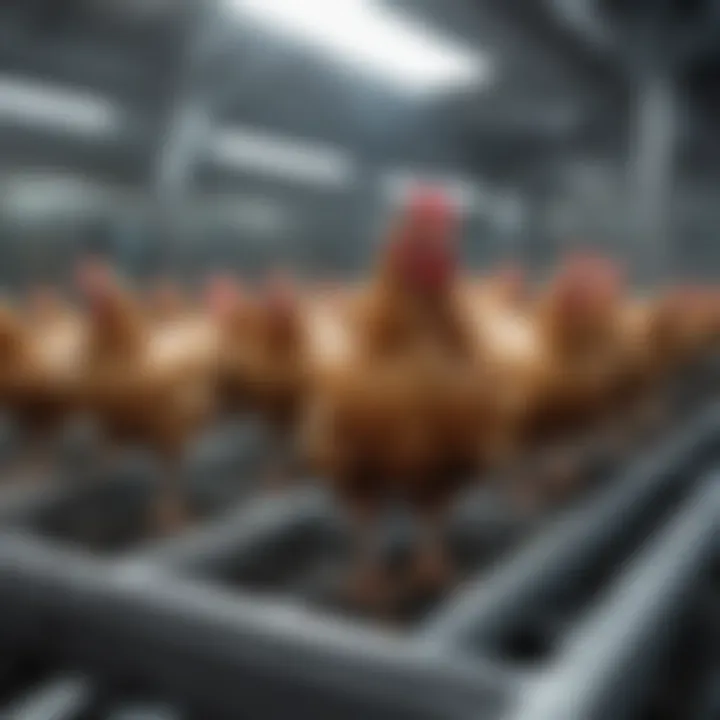
By prioritizing routine care, hatchery managers can maintain a high standard of incubation, ultimately leading to better productivity and reduced costs in poultry production.
Regulatory Standards for Hatchery Machines
Regulatory standards for hatchery machines play a crucial role in ensuring the safety and effectiveness of poultry farming operations. These regulations are established to protect the health of both the livestock and the consumers. By complying with established standards, hatchery operators can contribute to overall food safety and improve the well-being of their poultry.
Adhering to regulatory standards can seem complex, but it breaks down into a few key elements:
- Compliance with health and safety regulations to minimize risks to workers and animals.
- Meeting environmental compliance standards to ensure operations do not negatively impact the ecosystem.
- Following best practices in equipment maintenance and operation to ensure optimal performance.
The importance of these standards cannot be overstated. They help agricultural professionals to maintain high-quality production levels while fostering responsibility within the industry. Ultimately, compliance results in improved consumer confidence in poultry products.
Health and Safety Regulations
Health and safety regulations are vital to protect not only the hatchery workers but also the animals being raised. These regulations may include guidelines on the proper use of machinery, safety training for staff, and measures to prevent contamination or disease spread.
Regular training sessions for employees ensure that everyone can identify potential hazards. Personal protective equipment (PPE) is also mandated to reduce the risk of accidents or injuries during operation. Proper procedures for handling eggs and chicks are necessary to prevent injury to both the workers and the animals.
Furthermore, regulations often specify the need for thorough documentation. Keeping track of safety inspections, employee training, and machinery maintenance can help in case of audits. Following these guidelines minimizes risks and promotes a safe work environment for everyone involved.
Environmental Compliance Standards
Environmental compliance standards ensure that hatcheries operate sustainably and with minimal negative impacts on the surrounding ecosystem. This compliance involves managing waste efficiently, using resources wisely, and minimizing emissions.
To achieve these goals, hatchery operators often implement the following practices:
- Waste management plans that outline how to handle organic waste and chemicals safely.
- Water usage regulations to prevent over-extraction from local supplies or pollution of water sources.
- Energy efficiency measures to reduce the carbon footprint associated with hatchery operations.
Environmental standards shift the focus towards sustainable farming practices. By complying with these regulations, hatcheries can contribute positively to their communities and the planet.
"Adhering to regulatory standards is not just about compliance; it’s about evolving towards a sustainable future in agriculture."
Case Studies in Successful Hatchery Machine Implementation
Understanding how hatchery machines work in practical settings is crucial for assessing their effectiveness. This section explores real-world applications of hatchery technologies, focusing on small-scale farms and commercial hatcheries. These case studies illustrate the benefits and considerations relevant to various production scales, offering insight into the successful adoption of hatchery machines.
Small-Scale Farms
Small-scale farms significantly benefit from hatchery machines. They often face unique challenges, such as limited resources and lower production capacity. However, the implementation of hatchery technologies can lead to improved hatch rates and better control over incubation conditions.
For instance, a small poultry farm in rural Kentucky adopted a forced air incubator to manage its chicken egg hatching process. The farm owner noted a marked improvement in the hatch rate, which increased from 70% to 85% after integrating the technology. This change allowed the farm to meet local demand more effectively.
Moreover, the use of digital monitoring systems in hatchery machines has simplified operations. Farmers can now adjust temperature and humidity levels remotely. Such flexibility saves time and minimizes the risk of human error. As a result, small-scale farmers can focus on expanding their product offerings and improving overall efficiency.
Commercial Hatcheries
In commercial hatcheries, where scaled production is critical, hatchery machines play a pivotal role in maximizing output and ensuring high-quality chicks. A case study of a large commercial hatchery in California shows how advanced digital machines transformed their hatching process.
This facility implemented advanced automation and IoT integration to streamline operations. The automation reduced labor costs by 30%, as fewer workers were needed to monitor the incubators. Furthermore, the data analytics provided by IoT features enabled the hatchery to predict potential machine failures before they happened, leading to less downtime.
The hatchery also reported that implementing smart technology improved biosecurity measures. With real-time monitoring of environmental conditions, the hatchery could identify and mitigate risks swiftly, ensuring a healthier product. Such advancements in hatchery machines prove essential in maintaining competitive advantage in the poultry market.
"Successful hatchery machine implementation not only enhances hatch rates but also reduces operational complexities."
These case studies underscore the transformative potential of hatchery machines in both small and large-scale operations. Understanding these examples aids farmers in evaluating their options and optimizing hatchery practices. As hatchery technology evolves, ongoing assessment of real-world applications will remain valuable for industry practitioners.
The Future of Hatchery Machines
The realm of hatchery machines is at a transformative juncture. As we look ahead, it becomes clear that innovations will play a pivotal role in shaping these systems. The future of hatchery machines is significant. It reflects advancements in technology, efficiency, and sustainability that are essential for the agricultural industry.
Emerging technologies are streamlining design and functionality. This shift ensures smoother operations within commercial hatcheries. Not only do these innovations maximize hatch rates, but they also facilitate better resource management. The drive toward automation signals a move to decrease reliance on manual labor, which is especially critical amid labor shortages in agriculture.
Another crucial factor in the future of these machines is sustainability. As environmental concerns become more pressing, the importance of developing eco-friendly hatchery solutions intensifies. Enhanced energy efficiency and the use of renewable resources mark a new era in hatchery practices. Focusing on sustainable designs will not only benefit poultry farmers economically but also position them as responsible stewards of the environment.
"In the coming years, hatchery machines will evolve, integrating advanced technologies and sustainable practices to address both market demand and environmental concerns."
The benefits of these developments are manifold. Enhanced efficiency means lower operational costs and improved productivity. Sustainable practices align the poultry industry with global efforts toward reducing carbon footprints. These advancements in hatchery machines will help prepare farmers for future challenges while enhancing their competitiveness in a rapidly evolving market.
Trends in Machine Design
The trends in hatchery machine design are shifting toward advanced technologies that enhance functionality. Designs are becoming more compact, allowing efficiency in space utilization. Digital interfaces are occurring frequently, providing users with real-time data about the incubation environment. This technology enables better decision-making, helping farmers respond quickly to changing conditions.
Moreover, modular designs are gaining traction. These allow for easy upgrades and expansion as technology advances. Incorporating user-feedback into design ensures that machines continually evolve to meet users' needs. Integrating smart technology, such as IoT devices, into hatchery machines enhances data collection and monitoring, leading to optimized performance.
Sustainability in Hatchery Practices
Sustainability remains at the forefront of future hatchery practices. The usage of renewable energy sources in hatchery operations is expected to rise significantly. Implementing solar panels in hatchery facilities can drastically reduce energy costs and environmental impacts. Moreover, the selection of materials for manufacturing hatchery machines is shifting towards more sustainable options, promoting a circular economy in agricultural practices.
Water conservation techniques are also being prioritized. Efficient water usage strategies, such as rainwater harvesting and recycling systems, can minimize waste and provide clean water for the incubation processes. Taking these steps contributes to a more sustainable overall operation, addressing various ecological and regulatory pressures.