Understanding the Components of Gasoline Air Compressors
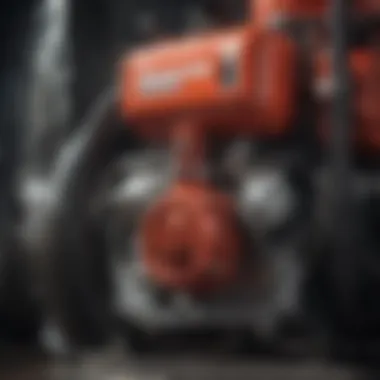
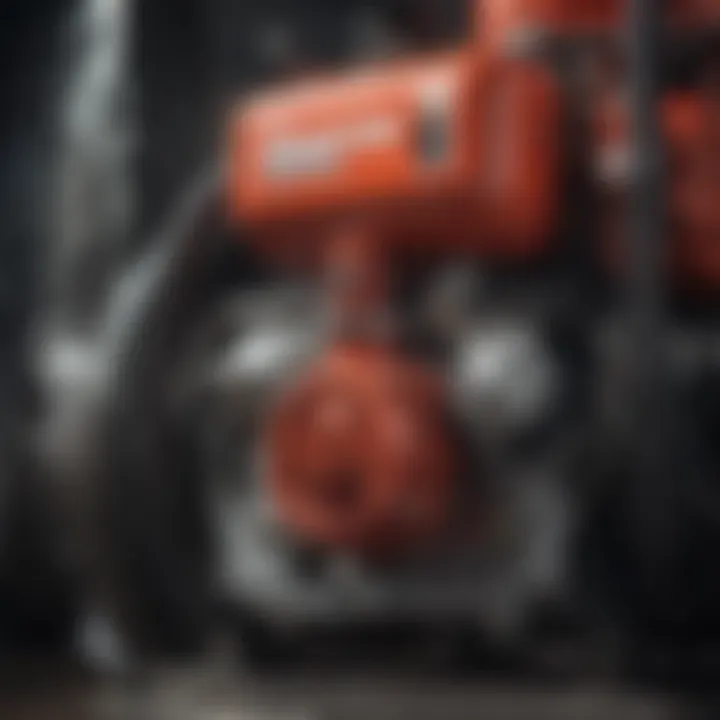
Intro
Gasoline air compressors play a significant role in various applications, especially in agriculture and horticulture. Understanding their components and how they function can greatly improve their usage and maintenance. This section delves into essential key concepts and terminology that form the core of gasoline air compressors.
Key Concepts and Terminology
Definition of Terms
Gasoline air compressors are machines that compress air and are powered by gasoline engines. They consist of several parts, each contributing to the overall performance and efficiency. Some common terms include:
- Compressor Pump: The main unit that increases air pressure.
- Engine: The gasoline-powered motor that drives the pump.
- Receiver Tank: Stores compressed air for later use.
- Regulator: Controls the pressure of the air being released.
- Hoses and Fittings: Connect various components for the transfer of compressed air.
Importance in Agriculture
In agriculture, the use of gasoline air compressors enables farmers to complete tasks efficiently. They power tools like pneumatic drills and impact wrenches, assist in maintaining machinery such as spray equipment, and facilitate irrigation systems. Efficiency is key in farming; therefore, understanding and maintaining these units can lead to better productivity and reduced downtime.
Current Trends and Innovations
Technological Advancements
Recent improvements in gasoline air compressors focus on efficiency and ease of use. Modern compressors come equipped with advanced technology, such as:
- Inverter Technology: Matches output with demand, reducing fuel consumption.
- Noise Reduction Features: Quieter operations make them suitable for residential areas.
Sustainable Practices
Sustainable practices are gaining significance in farm management. Farmers are adopting more energy-efficient models that reduce greenhouse gas emissions. Additionally, the focus on safety measures has increased, with features that prevent fuel spills and exhaust leaks, ensuring a cleaner and safer working environment.
Best Practices and Techniques
Step-by-Step Guides
To operate and maintain gasoline air compressors effectively, follow these best practices:
- Regular Inspection: Check oil levels, air filters, and hoses for any signs of wear.
- Fuel Maintenance: Use clean, suitable fuel; avoid mixing different types of gasoline.
- Proper Storage: Store the compressor in a cool, dry place when not in use.
Tools and Resources
Access to the right tools is crucial for maintenance tasks. Common tools may include:
- Adjustable wrench
- Oil change kits
- Air filter replacement kits
Resources such as guides available on Wikipedia can provide additional insights into specific models or troubleshooting tips. Engage with communities on Reddit for shared experiences and advice directly from other users.
Improve your familiarity with each component of your gasoline air compressor for more efficient usage.
Achieving a complete understanding of these vital machines can augment their functionality and reliability, making them invaluable assets in agricultural practices. By keeping these components and practices in mind, both novice and experienced users can enhance their efficiency and effectiveness.
Prelims to Gasoline Air Compressors
Gasoline air compressors are essential tools in various sectors, particularly agriculture. These machines supply compressed air for diverse applications, rendering them indispensable for efficient operations. Understanding their components and functions allows users to maximize their performance and troubleshoot issues effectively. In this section, we will explore the definition, significance, and uses of gasoline air compressors.
Definition and Function
Gasoline air compressors convert gasoline fuel into mechanical energy to compress air. This process involves drawing in air, compressing it, and storing it for later use. The key function is to provide a reliable source of compressed air required for several tasks. These can range from inflating tires to powering pneumatic tools. Understanding the basic mechanics helps users appreciate the complexity and efficiency of these compressors.
Gasoline engines power most of these compressors, making them versatile and suitable for remote operations where electricity is unavailable. They are known for their mobility and efficiency. As tasks vary by application, knowing the specifics of how each part contributes to the overall function is crucial.
Applications in Agriculture
In agriculture, gasoline air compressors serve multiple purposes. They are commonly used for pumping water, spraying pesticides, and powering various tools. Their role in irrigation systems is noteworthy. Compressed air can be utilized to move water in pressurized systems, facilitating efficient watering of crops. The ability to work in off-grid areas is significant, providing farmers essential equipment without the need for power grids.
Key applications include:
- Crop Spraying: Farmers utilize these compressors to ensure even application of fertilizers and pesticides, ensuring crop health.
- Pneumatic Tools: Many farmers employ pneumatic tools powered by air compressors for repairing equipment or assembling farm structures.
- Water Transportation: In remote farms, gasoline air compressors can aid in transporting water, crucial for crop maintenance.
Understanding these applications enriches one's knowledge of how gasoline air compressors contribute to efficient agricultural practices and productivity.
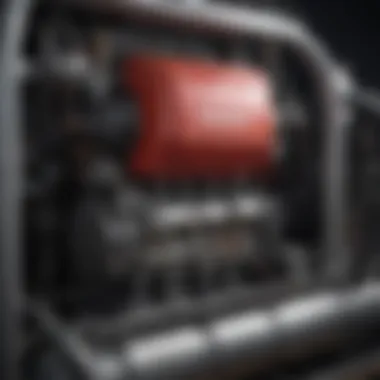
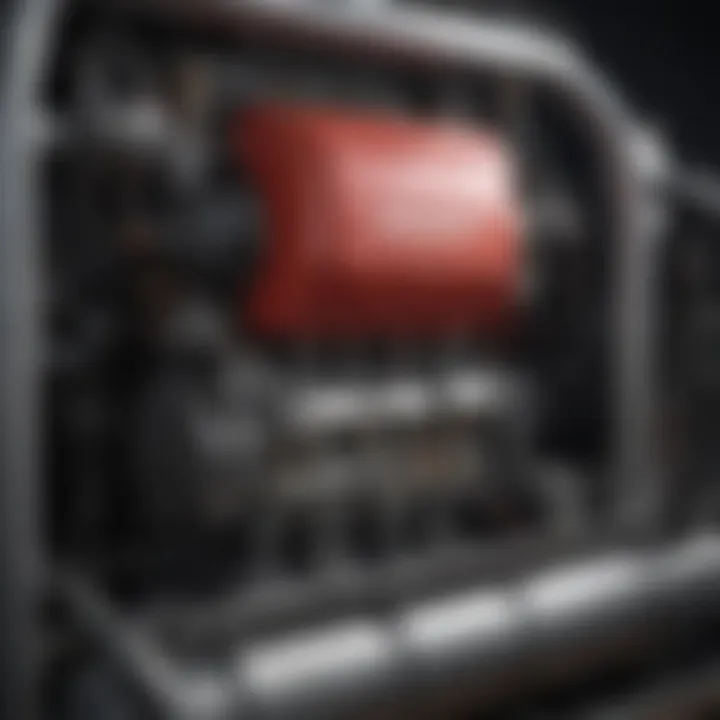
Main Components of Gasoline Air Compressors
Gasoline air compressors consist of several critical components that directly influence their efficiency and functionality. Understanding these parts is essential not only for operational awareness but also for effective maintenance and troubleshooting. Each component plays a pivotal role. Knowing how they work together can significantly enhance the use of these machines in agricultural settings.
Compressor Pump
The compressor pump is arguably the heart of the gasoline air compressor. Its primary function is to convert mechanical energy from the engine into air pressure.
Types of compressor pumps
There are several types of compressor pumps, including reciprocating and rotary screw pumps. The most common in small gasoline air compressors is the reciprocating pump, known for its durability and ease of maintenance. This pump type has a straightforward design, allowing users to perform repairs and replacements with relative ease.
The key characteristic of reciprocating pumps is their ability to provide high pressure in a compact design. They are ideal for applications requiring immediate airflow, making them popular for tasks in agriculture, such as inflating tires or powering pneumatic tools. However, they may be less efficient than rotary pumps for continuous operation, as the high-pressure cycles can create wear over time.
Maintenance tips
Regular maintenance of the compressor pump ensures longevity and efficient operation. Some essential tips include checking for air leaks, ensuring the pump is appropriately lubricated, and monitoring for unusual noises that may indicate wear. The unique feature of proactive maintenance is that it can prevent costly breakdowns. Neglecting these practices could lead to reduced performance or complete failure of the pump at critical moments.
Engine
The engine serves as the power source, driving the compressor pump. Understanding engine specifications can help ensure optimal performance.
Gasoline engine specifications
The most common types are 4-stroke gasoline engines, favored for their fuel efficiency and lower emissions. When selecting an engine for a compressor, consider its horsepower, which significantly impacts air output. The main characteristic is that the engine must be appropriate to the demands of the compressor.
The unique aspect of gasoline engines in this context is their portability compared to electric motors. This makes them suitable for use in remote agricultural locations where power sources are unavailable. However, gasoline engines often require more maintenance due to their fuel type, which can lead to issues like carburetor clogging or fuel line degradation.
Common issues and troubleshooting
Common issues include starting difficulties and irregular power output. When troubleshooting, it is important to check fuel levels, connections, and the battery. Another significant issue is overheating, often caused by inadequate airflow or excessive load on the compressor. Understanding these challenges and their solutions can save time and resources during operation.
Air Tank
The air tank stores compressed air, playing a crucial role in providing a steady and reliable air supply for various tasks.
Capacity considerations
Tank capacity is a vital consideration and usually comes measured in gallons. A larger tank can store more air, enabling longer usage periods between engine runs. This is particularly advantageous for agricultural applications where continuous air supply is needed for tools and sprayers. However, larger tanks can also make the compressor heavier and less portable.
Inspection and care
Routine inspection of the air tank is necessary to ensure safety and functionality. Checking for rust, leaks, and ensuring proper pressure levels are all essential maintenance steps. The advantage of regular inspection is that it can catch problems early, before they necessitate more extensive repairs. On the downside, neglecting these inspections can put users at risk if a compromised tank bursts due to over-pressurization.
Pressure Regulator
The pressure regulator is vital for controlling air pressure levels, ensuring they remain within safe and effective limits.
Role in operation
The regulator's main role is to maintain a constant air pressure supply to tools connected to the compressor. It does this by automatically adjusting the airflow based on the tool's requirements. The ability to maintain steady pressure prevents tool damage from excessive air pressure, which is crucial in delicate agricultural tasks.
Adjustment and calibration
Regularly adjusting and calibrating the pressure regulator ensures ideal performance. Users should refer to the manufacturer’s guidelines for recommended pressure settings. Proper adjustments help ensure efficiency and can prevent accidents or equipment damage. A carefully calibrated regulator can maximize tool performance, yet improper settings can lead to poor outcomes in practical applications.
Hoses and Fittings
Hoses and fittings are essential for delivering compressed air from the compressor to the tools. Their condition can greatly impact efficiency.
Material types
Common materials for hoses include rubber and polyurethane. Rubber hoses are often more durable and resistant to weather conditions, making them suitable for outdoor agricultural tasks. However, they can be heavier than their polyurethane counterparts, which are lighter and more flexible but may wear faster under extreme conditions.
The characteristic selection of materials can affect both efficiency and safety. Users must choose hoses that can handle their specific air pressure requirements while also considering weight and flexibility for ease of use.
Safety measures
Safety measures in handling hoses include regular inspections for cracks or leaks. Adequate storage practices prevent kinking and damage when not in use. Another important aspect is to ensure proper fittings are used, as loose connections can lead to dangerous air leaks under pressure. Prioritizing safety in these components can prevent accidents and extend the lifespan of the hoses and fittings.
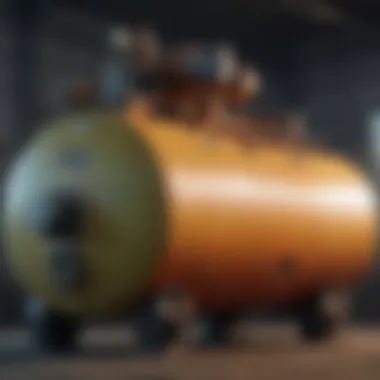
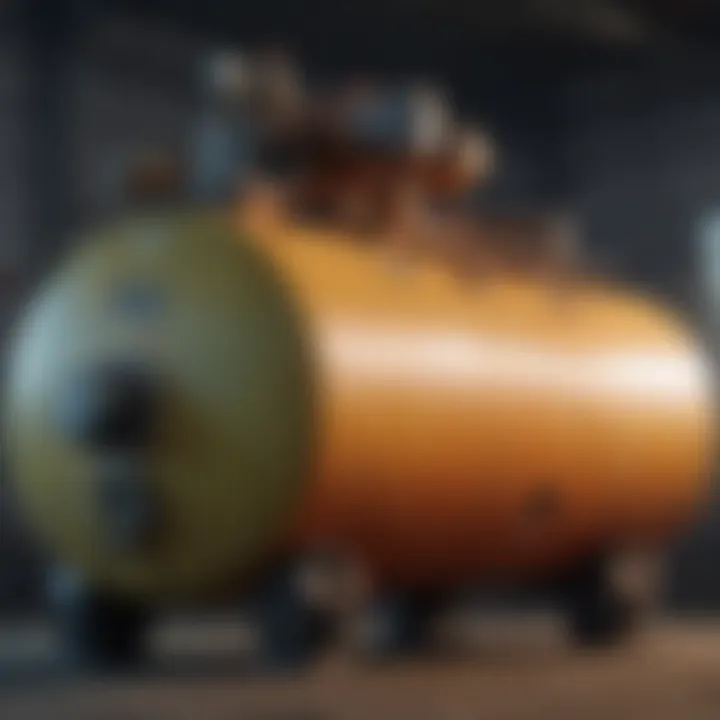
Supplementary Components
Supplementary components are critical for the overall performance of gasoline air compressors. These parts work to enhance functionality, improve efficiency, and ensure the device runs smoothly. Understanding these supplementary components allows users to make informed decisions about maintenance and operation.
Air Filter
Importance of filtration
Filtration is essential in maintaining the quality of air that the compressor uses. A clean air filter ensures that dust, debris, and contaminants do not enter the compressor. This aspect is particularly significant when using the compressor in environments with a lot of dirt, such as agricultural fields. Key characteristics of proper filtration include enhancing engine efficiency and prolonging the lifespan of internal components. A good filter can capture particles as small as five microns, making it a beneficial choice that prevents costly repairs and downtime.
Replacement intervals
Regularly replacing the air filter is paramount. Keeping track of replacement intervals ensures that the compressor continues to operate effectively. Depending on usage and the environment, filters may require changing every 50 to 100 hours of operation. A unique feature of these intervals is their adaptability; users can adjust based on performance monitoring. The advantage of keeping a consistent replacement schedule is the assurance of uninterrupted air delivery and optimal performance.
Oil Separator
Functionality
The oil separator plays a vital role in maintaining the cleanliness of the compressed air. It prevents oil from mixing with the air that is discharged from the compressor. This functionality is crucial since oil contamination can disrupt equipment that relies on air from the compressor. Key characteristics include ensuring clean air that meets operational standards. Implementing a quality oil separator is beneficial, as it directly impacts the reliability of the entire system.
Maintenance guidelines
Proper maintenance of the oil separator is necessary to maximize its efficiency. Recommendations suggest inspecting the separator regularly, at least every 100 hours of operation. Cleaning or replacing the component as needed prevents buildup of contaminants that can impair its function. A unique aspect of these maintenance guidelines is their straightforwardness, which allows even novice users to perform simple checks. The advantage here is that proactive management can help avoid complete system failures and extend the unit's life.
Cooling System
Circuit design
The cooling system in a gasoline air compressor is designed to manage the heat generated during operation. A well-structured circuit design allows for efficient heat dissipation, ensuring that components do not overheat. Key features of this design include adequate airflow and strategically placed cooling fins that enhance thermal management. A well-designed cooling system is beneficial because it helps maintain optimal operating temperatures, which is crucial for performance and longevity.
Troubleshooting overheating
Overheating can pose serious risks to compressor operation. Understanding how to identify signs of overheating is valuable for maintaining functionality. Common symptoms include unusual noises, decreased performance, and visible smoke. Users should regularly monitor temperature gauges and clean any obstructions in the ventilation areas. The specific aspect of troubleshooting overheating lies in its straightforward approach — users can often resolve these issues without professional assistance. The advantage of being vigilant about overheating is the prevention of more severe damages that can lead to costly repairs.
Maintenance Practices for Optimal Performance
Maintaining gasoline air compressors is essential for their longevity and effectiveness, especially in high-demand environments like agriculture. Regular maintenance minimizes the risk of breakdowns and ensures that compressors deliver optimal airflow and pressure.
Key elements of maintenance include regular inspections and proper lubrication. Each of these practices plays a significant role in enhancing performance, reliability, and safety.
Regular Inspections
Conducting inspections regularly is critical in identifying potential issues before they escalate. This proactive approach preserves the functionality of the air compressor, which can save time and money down the line.
Checklist for Parts
Having a thorough checklist for parts is a cornerstone of efficient maintenance. It ensures that all crucial components are inspected systematically. The key characteristic of a checklist is its comprehensiveness, making it easy to track the conditions of various parts like hoses, fittings, filters, and the pressure regulator. It is a beneficial choice for this article, as it emphasizes the importance of methodical checks.
The unique feature of using a checklist lies in its structured approach. By covering each section methodically, users can quickly identify areas needing attention. This is particularly advantageous as it reduces the likelihood of overlooking critical components, thus fostering efficient functioning of the air compressor.
Signs of Wear and Tear
Recognizing signs of wear and tear is vital for timely intervention. When parts start to wear, it can lead to performance issues. The key characteristic here is the ability to spot these signs early. This proactive recognition assists in preventing catastrophic failures.
This approach is a popular choice for this article because it promotes awareness among users. It empowers them to take action quickly, addressing issues before they become severe.
A unique feature of monitoring wear and tear is the focus on specific indicators such as unusual sounds, leaking oil, or diminished pressure. Being vigilant about these signs has significant advantages, as early detection can lead to easy repairs rather than costly replacements.
Lubrication
Lubrication is critical for the smooth operation of gasoline air compressors. It minimizes friction, reduces wear, and ultimately prolongs the lifespan of components.
Types of Lubricants
Understanding available types of lubricants is pivotal. Synthetic and mineral oils are common options. The key characteristic of synthetic oils is their resistance to breakdown, providing superior lubrication under extreme conditions. This makes them a beneficial choice for compressors operating in demanding environments, particularly in agriculture.
A unique feature of synthetic lubricants is their ability to maintain viscosity over a wide temperature range. This advantage is essential, as consistency leads to effective performance and fewer malfunctions.
How Often to Lubricate
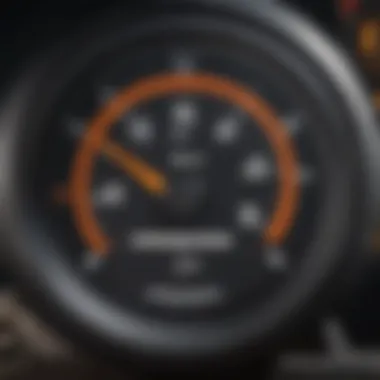
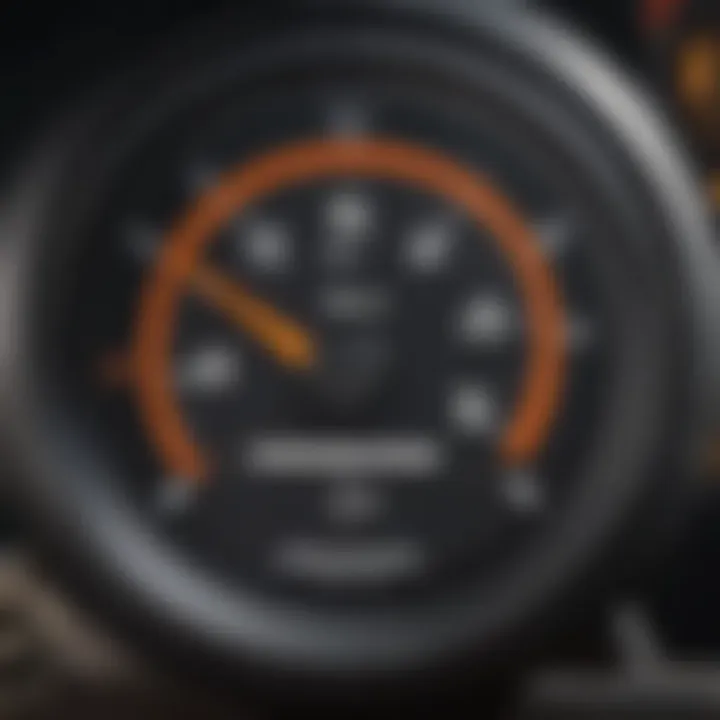
Determining how often to lubricate is equally crucial for maintaining air compressors. Regular lubrication intervals prevent excessive wear and ensure all parts operate smoothly. The key characteristic of a well-timed lubrication schedule is that it aligns with the operational conditions of the compressor.
It is a popular choice for this article because consistency in lubrication directly correlates with performance. A regular schedule, like lubricating every 50 hours of operation, can be effective in reducing malfunctions.
A unique feature of establishing a lubrication routine is its adaptability. Users can adjust their frequency depending on the compressor's workload. This custom approach has distinct advantages, as it ensures lubrication is adequate for varying operational demands.
Remember, timely maintenance practices can greatly enhance the efficiency and reliability of your gasoline air compressor.
In essence, adhering to these maintenance practices, including regular inspections and proper lubrication, is crucial for ensuring optimal performance of gasoline air compressors. By investing time and effort in maintenance, users can enjoy a more efficient and reliable air compressor, leading to successful operations in agriculture.
Troubleshooting Common Issues
Troubleshooting common issues is essential when operating gasoline air compressors. Addressing problems quickly ensures smooth functionality and prolongs the lifespan of the machine. This section focuses on specific engine and air delivery issues. Understanding how to diagnose and remedy these problems helps users maintain optimal performance in agriculture and horticulture applications.
Engine Problems
Starting difficulties
Starting difficulties can frustrate users of gasoline air compressors. This issue commonly stems from various factors, including battery conditions, ignition systems, or even fuel quality. The significance of this aspect lies in its direct impact on efficiency and productivity. If a compressor fails to start, work schedules can be disrupted, especially in agriculture where time is vital.
A common characteristic is the inability of the engine to turn over or make a noise when engaging. This situation is often the first sign that something needs attention. A beneficial approach in this case is a systematic check of electrical components and fuel lines.
Unique features such as the presence of a choke or starter mechanisms can also affect the compression process. Their proper function contributes significantly to reliable starting, while neglect can result in repeated failures.
Fuel-related issues
Fuel-related issues are another critical element in maintaining the efficiency of gasoline air compressors. Problems can arise from improper fuel types, contamination, or degradation over time. This aspect affects overall performance as fuel quality impacts combustion and, subsequently, engine operation.
Notably, a common characteristic of fuel-related problems includes irregular engine performance or unexpected shutdowns. This makes addressing it a necessity for ensuring reliability in demanding applications, such as in agricultural tasks.
A unique feature involves additives that can enhance fuel quality and prevent engine knocking. While some users favor lower-cost options, the consequences of poor fuel can be higher repair costs in the long run.
Air Delivery Issues
Low pressure concerns
Low pressure concerns can significantly hinder the effectiveness of a gasoline air compressor. This issue often indicates potential leaks or mechanical failures in components responsible for air delivery. The importance of addressing these concerns lies in the compressor's primary function: to deliver sufficient pressure for effective operation.
A key characteristic of low-pressure incidents is the drop in output performance during usage, which can lead to insufficient airflow for tools requiring pressurized air. Users may notice a decrease in efficiency, leading to frustrations in work.
Unique features, such as pressure gauges, play a crucial role in helping users monitor performance. Regular checks can prevent severe issues and maintain operational standards. Not identifying low-pressure conditions early may result in more significant, costlier repairs.
Leak detection
Leak detection is vital to ensuring a gasoline air compressor operates efficiently. Detecting leaks early helps maintain performance and extend equipment life. Over time, wear and tear may cause connections to deteriorate, leading to air escape and lower operational efficiency.
A key characteristic is the ability to identify hissing sounds or visible air escape, which can indicate a problem area. Choosing to pursue leak detection is beneficial, as early intervention saves time and resources in repairs.
One effective method is using a mixture of soap and water to spot bubbles at connection points. This method provides a straightforward and economical way to assess leaks. Ignoring small leaks can escalate issues, leading to more complex repairs, and significantly decreasing the compressor's effectiveness over time.
"Regular maintenance and timely troubleshooting are essential for maximizing the performance of gasoline air compressors in agricultural and horticultural tasks."
Culmination
The conclusion of this article serves as a crucial synthesis of the various components and maintenance considerations that contribute to the functionality of gasoline air compressors. Effectively, it encapsulates the main insights and recommendations derived from the detailed exploration of each part. Understanding these elements enables users, especially those in agriculture, to make informed decisions regarding the selection and upkeep of these machines.
Key points to consider in this conclusion include:
- Comprehensive knowledge of parts: Familiarity with components such as the compressor pump, engine, air tank, and pressure regulator is essential for optimal performance.
- Maintenance practices: Regular inspections and lubrication are critical to prevent issues that could lead to inefficiencies or operational failure.
- Troubleshooting: Understanding common problems and their solutions allows users to manage potential downtimes effectively.
By summarizing these aspects, the conclusion underscores the importance of proactive maintenance and a solid grasp of how each part interacts within the larger system of the gasoline air compressor. This understanding ultimately translates into a more effective application in agricultural practices, enhancing productivity and reducing interruptions.
Summary of Key Points
The key points covered throughout this article are as follows:
- Components with Distinct Roles: Each part of the gasoline air compressor plays a specific role, impacting overall performance.
- Regular Maintenance Affects Longevity: Systematic inspections, lubrication, and care contribute significantly to the lifespan of the compressor.
- Troubleshooting Common Issues Adds Efficiency: Identifying and resolving issues, such as engine difficulties or air delivery concerns, is essential for seamless operations.
- Applicability in Agriculture: Understanding these concepts is particularly beneficial for farmers and agricultural enthusiasts aiming to maximize the utility of their equipment.
Future Considerations
Looking ahead, several future considerations arise in the context of gasoline air compressors:
- Technological Advancements: New technologies may introduce improved components or features that enhance efficiency and reduce energy consumption.
- Sustainability Practices: Considering the environmental impact of gasoline engines, trends toward more eco-friendly options should be evaluated.
- Training and Education: Ongoing education on best practices in maintenance and operation will remain vital as machinery evolves.
Overall, the future of gasoline air compressors will likely be shaped by a combination of user demands, technological innovations, and environmental concerns. Being attuned to these changes will allow users to adapt and maintain optimal performance for years to come.